Correcting seal failures
R. David Whitby | TLT Worldwide July 2009
Determining the cause of the problem and taking appropriate action will help your company’s bottom line.
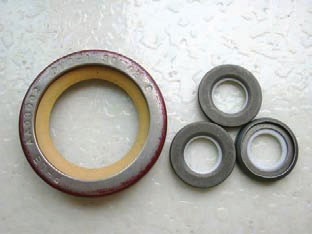
Selecting the correct seal is only the beginning of sound equipment operation.
In May we discussed why seals are vital to the maintenance of operating machinery. Unfortunately, seals can either wear out or fail.
To determine whether a seal has worn or failed, the wearable face should be examined. For most lip seals this is the face manufactured from some type of elastomer (rubber). Since the seal face is the only sacrificial part of a mechanical seal, a worn out seal has no elastomer nose piece left at the time it started to leak. A failed seal still has substantial elastomer remaining at the time it started to leak.
Seals can fail for numerous reasons, including poor lubrication. Standard lip seals are particularly vulnerable. Most consumers experience seal failure rates in excess of 85%, and for the most part these seal failures are avoidable. Seal failures fall into only two broad categories: either the seal faces opened or one of the seal components was damaged by contact, heat or corrosion.
Types of elastomeric seal failures include hardening, wear, scarring, swelling, cracking, grooving, extrusion and fracturing. The causes can include insufficient lubrication, excessive temperature, absorption of fluids, metal or dirt contaminants, excessive back pressure, excessive lateral loads and frequent high pressure shocks.
The Practical Handbook of Machinery Lubrication, published in 2005 by Maintenance Technology International, contains helpful information for lubrication engineers on the reasons for seal failures and what to do about them.
Following are reasons for seal failures:
•
Misalignment of components
•
Poor bearing lubrication
•
Vibration of rotating components
•
Contaminated fluid (water, acids or particulate)
•
Twisting condition due to “soft foot” at mounting pads
•
Poor component base plate grouting or mounting
•
Rotor imbalance or shaft whip
•
Inadequate flushing procedures during commissioning or startup after repairs
•
Poor or careless seal (or bearing installation)
•
Piping strains due to misalignment or temperature variations
•
Looseness of bolts and brackets
•
Addition of incompatible fluid
•
An increase in temperature (or a dramatic change in temperature)
•
Unclean operating conditions (dirt ingression)
•
A change in filtration practices.
Oil seals for rotating or reciprocating shafts require a degree of lubrication of the moving surfaces. Oil seals must never run dry.
Cost-cutting by machine design engineers, incomplete commissioning and plant start-up procedures and inadequate equipment, condition monitoring and maintenance practices are the major reasons for initial seal failure and fluid leakage.
A used seal having a shiny wear flat with hardening and radial cracking is indicative that it had operated on a shaft that was too smooth and/or the radial load exerted by the lip was too high. A used seal having a wide wear flat likely operated on a shaft that was too rough, especially if there was no hardening or radial cracking. Or there could have been an issue with incorrect sealing lip geometry.
Once a seal has failed and fluid leakage results, the problem is perpetuated by bad purchasing department policies of restocking less expensive (that is, low quality) seals, continuing to use incorrect seals or by careless installation practices used during replacement procedures. The subsequent leaks, while not considered excessive, go on and on and soon plant operating and maintenance personnel accept the leakage as normal.
When a seal fails, don’t just replace it. The real cause of failure needs to be determined and appropriate remedial action taken. Remember that the seal is there to keep the lubricant in and dust, dirt and water out of the operating equipment.
Selecting the correct seal is only the beginning of sound equipment operation. Ongoing predictive condition monitoring using vibration and fluid analysis, a regular review of equipment operating logs and the implementation of a sound preventive maintenance program will ensure the long life of seals, eliminating leaks and environmental damage. It also adds millions of dollars to the bottom line.
David Whitby is chief executive of Pathmaster Marketing Ltd. in Surrey, England. You can reach him at pathmaster@dial.pipex.com.