Test efficacy in oil analysis
Jack Poley | TLT On Condition Monitoring July 2009
There are a variety of methodologies available to provide you with the best options for your program.
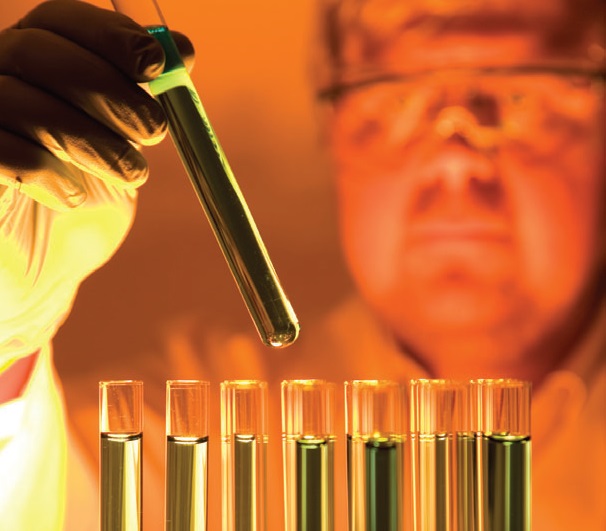
Oil analysis consists of a variety of selected tests, which reveal information that can be assessed for practical maintenance decisions.
www.canstockphoto.com
In recent columns we’ve addressed the fact that oil analysis is cheaper and implied that overall it was also better. But what does better mean?
Oil analysis consists of a variety of selected tests that reveal accessible information for practical maintenance decisions. Previously, I’ve discussed that most information tested for has remained the same over four decades, but the testing methods changed due to development of increasingly sophisticated instrumentation. Such development added desirable capabilities and reduced costs.
Following are some of the benefits achieved by converting traditional methods to computerized instruments:
•
Sample size and cost of disposal reduced
•
Multiple results available from a single analysis
•
Automation is often available, saving labor
•
Computers facilitate data uploading, resulting in labor savings and minimal input errors; less chance for analytical error, as well.
DISADVANTAGES OF TESTING METHODS
•
Many of today’s instrumental tests are inductive in nature, in that the result of interest is an indirect, rather than direct, measurement. At times a new oil reference sample is required, and an assumption must be made that no interfering chemistry exists in the used sample. Such assumption is usually valid, or perhaps better put, sufficient. However, there are times when the matrix of the sample, or an unexpected property or contaminant, may result in false referencing. Corollary: If a reference new oil sample is required but is not available, results can be suspect.
•
In developing instruments to reduce cost, weight or footprint, there may have been some compromise in resolution* to achieve such goals, possibly affecting detection sensitivity at low levels. Most times this is OK, though components normally showing low concentrations for the result of interest will be slightly more difficult to assess with respect to that property, perhaps clouding the overall evaluation.
Here are some notions along those lines:
•
Iron (Fe) concentration can be determined in several ways. Each of these methods is distinctly different, and it is unlikely one can achieve direct correlation between methods in most circumstances, e.g.:
o
Wet chemistry. This method is the only one that is absolutely holistic, as it is performed in total solution,** not influenced by particle size, matrix, density and other factors.
o
Ultraviolet spectrum spectroscopy (UVS). UVS is regarded as the current standard, but a variety of techniques within this method is available: atomic absorption; emission spectroscopy, with both arc-spark and inductively coupled plasma excitation sources; and samples run neat or diluted. Regardless, they all share the same limitation in that they are unable to detect particulates much beyond five micrometers, so there is no reason to expect correlation with wet chemistry.
Another significant concern with UVS is the composition of the oil’s basestock—its matrix. Carbon and hydrogen are typical spectral reference lines, thus a synthetic fluid creates a significantly different spectrum influence such that reference standards in the matrix to be analyzed may be necessary in order to achieve reliable results. As a practical matter, this is rarely done, except in very specific situations.
o
X-ray fluorescence (XRF). Samples are run neat, bombarded with X-ray energy which will fluoresce in proportion to various elements of interest, including iron. Particle size is not as big a factor as with UVS, but it is not entirely negligible, either. In any event, this is yet another form of spectroscopy, quite differentiated from UVS.
o
Magnetometry. A relatively newer technology applied to oil analysis, including an instrument recently introduced, determining parts-per-million iron concentration as iron, the metal. This is clearly different from the previous methods as iron must be in metallic (magnetic) form to be detectable. Ferric oxide (rust) would not qualify. Further, standards for this instrument must be iron-metal in an epoxy medium as metallo-organic liquid standards, normally utilized for calibration in the methods previously listed, would not impart any magnetic flux. While this method would not be expected to correlate with others mentioned herein, it does address the wear aspect of iron quite specifically, and its output can be used as a repeatable comparator, particularly for large particle sizes missed by UVS.
•
Infrared spectroscopy (FTIR – Fourier Transforms IR) has achieved ubiquitous use in a variety of contexts, resulting in copious data output. Some of the properties examined, however, pose particular challenges:
o
Fuel soot. An important datum for diesel engine oils, the technique is based on light scattering and absorption in a broad area of the spectrum. This produces acceptable results most of the time but does not compare to the direct method of thermogravimetric analysis (TGA), often used to calibrate IR data. There is also the issue of effective range, particularly at high soot levels (>8%).
o
Fuel. It is very similar to hydrocarbon oils, though possessing a shorter carbon chain. Differentiating fuel from oil, therefore, is quite an exercise in detection using infrared technology. There are several other methods that are significantly more effective much of the time. To get IR to its most efficient level requires samples of the fuel being used to achieve the tightest baseline referencing, something that is, at times, impractical.
SUMMARY
1.
Some compromises in detectability and precision may exist in any given instrumental method. As such different methods, even though they are designed to achieve the same property measurement, may not yield comparable data, yet both may be sufficient for the job at hand. Corollary: Once a method is selected, stay with it.
2.
For the most part, the inherent compromises resulting from technological innovation have usually been well considered and offer enough gains in information, speed and cost-per-test to offset some losses in detection and precision. Corollary: Before embarking on or revising a program, take proper time to consider your specific needs (which should largely be governed by the types and criticality of equipment you are monitoring). If necessary, get professional help. Ask questions and be sure you’re comfortable with the answers.
3.
Because the information sought may be at fringe levels, it is
vital to properly calibrate and standardize these sophisticated instruments in accordance with manufacturers’ requirements and recommendations. It is very easy to lose discipline in this area, and the possibility of generating bad data then becomes very real. The keys are:
(a) Due diligence in calibrating, maintaining and standardizing one’s instrumentation.
(b) Striving to have pertinent, current new oil references and standards to allow these instruments to provide their best output.
* Semiautomated spectrometric metals analysis provides the backbone for routine wear assessment in machinery. The original instrument was about nine feet in length, providing a much greater spectrum spread than today’s compact instruments. Although the electronics are far more sophisticated, the actual resolution of the spectrum is somewhat less (though certainly not fatal).
** It is possible to ash an oil sample, then dissolve the ash in acid, resulting in a complete solution that can be analyzed via UVS, an exception to the rule, but usually impractical unless performing a failure analysis or other special circumstance, as such a process is time consuming, also requiring a higher level of skill than the basic operation of an instrument designed for convenience and speed.
Jack Poley is managing partner of Condition Monitoring International (CMI), Miami, consultants in fluid analysis. You can reach him at jpoley@conditionmonitoringintl.com.
For more information about CMI, visit www.conditionmonitoringintl.com.