Lessons from home
Peter A. Oglevie | TLT Shop Floor June 2009
Sometimes we have to learn the hard way that people are part of the system, too.
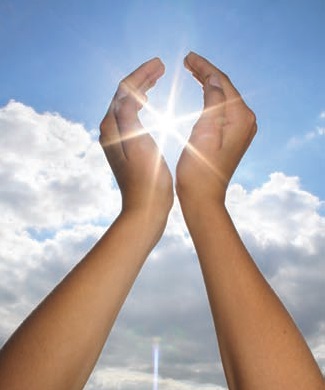
Mom was the one who taught me patience and understanding.
www.canstockphoto.com
Much of what I am is the product of the lessons learned from my parents. Dad always told me, if you have to do a job, do it to the best of your abilities. He was also the man who taught me much of what I know about the shop floor and manufacturing processes.
Mom was the one who taught me patience and understanding. They both taught me that if you fail you get back up and try again. They both taught me to look for the good in everyone. Their lessons bring to mind a bittersweet shop floor story.
I used to work with a muffler company that had seven plants spread over an entire state. I called on these plants every month, which meant a two-day trip and keeping a schedule to get all of the work completed. Many of these plants had similar processes and equipment modified to the product line they were responsible for. One process common to several plants was perforating and forming baffle tubes.
On one of my monthly trips I was at the end of a day and behind schedule. I was just getting into the last plant at 6:30 in the evening. I had called ahead and was told to work with Sam, the night foreman, and that they were having problems with the baffle tube process. When I arrived, Sam was glad to see me, and we got to work.
Sam took me to see what he perceived to be the problem, the welding line. Sam started by explaining how the welds were too porous. I noticed oily blanks and smoke in the air around the machines. Sam asked why he was having problems while the other plants weren’t. A lesson dad had taught came to mind. “If you don’t control the lubricant, you can’t control the process.” I suggested to Sam we look upstream in the process to find the cause of the problem.
Sam and I went to the perforating machine where the original flat blanks for the baffle tube were perforated. Based on the amount of oil and smoke we had seen at the weld station, I suggested we look at the emulsion concentration and the amount being applied. When we checked we found the concentration at 33%, and the volume turned to almost full (5 cc per stroke). I could see he was using at least three times more oil concentrate than was necessary.
I asked Sam about this, and he told me the spray system didn’t work unless turned all the way up. Since tool life was down, he had ordered an increase in concentration. I realized at that moment that I was in for several hours of work on top of an already-long day.
At that point my main desire was getting to bed so I could get an early start the next day. So instead of explaining everything to Sam, I just started to work at the perforating machine to readjust the concentration (15%) and the volume from the pump (1.5 cc per stroke). Taking the pump system apart and putting it back together again took two hours. At about 9 p.m. I had the system ready to go into operation.
I got Sam back over to the perforating machine, which now was performing up to spec. Sam pointed out that the parts were coming off cooler, cleaner and the slugs weren’t pulling anymore. The parts welded with no problems, and the smoky air was gone.
However, instead of being gracious and explaining everything I had done, I started telling Sam everything he had done wrong. In particular, I told him he was wrong to increase the concentration and volume.
Sam finally interrupted and asked why I was being so hard on him. He pointed out that no one had ever given him these instructions. I realized I had broken one of Mom’s golden rules. I had fixed and controlled the process like dad had taught me, but I’d forgotten Mom’s lessons about patience and understanding. Sam was glad to see me leave.
Mom, sometimes we have to learn the hard way. Thank you for your patience and understanding. May you rest in peace. (
Editor’s note: Pete Oglevie’s mother passed away in late March.)
Pete Oglevie is president of International Production Technologies in Port Washington, Wis. You can reach him at poglevie@intprotec.com.