Waste treatment in tough times
Dr. Robert M. Gresham, Contributing Editor | TLT Lubrication Fundamentals June 2009
You can reduce operating costs and help the environment—providing your plan is global in its approach.
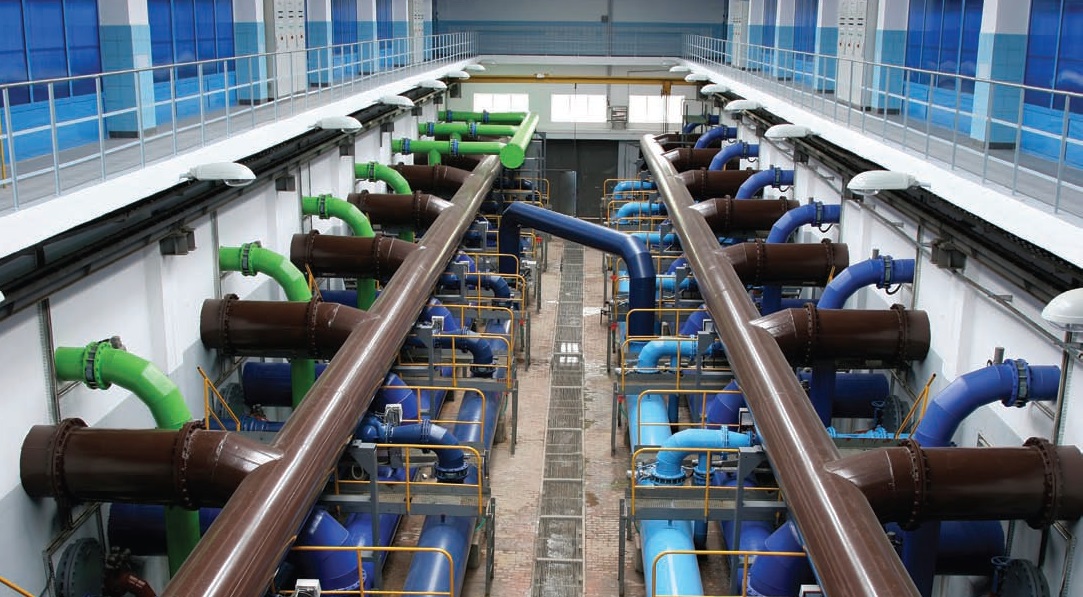
KEY CONCEPTS
• A well-conceived plan can reduce lubricant purchases, lower waste treatment costs, help the environment and eliminate a negative societal image.
• Recycling only makes sense when a global business case can be made for it.
• Too many plant operations people are not aware of the issues affecting the operation of the waste treatment plant.
During tough times it’s important for managers to stay focused and disciplined regarding the things that made their company successful during the good times. This is not to say you don’t embrace positive change or hang on to old things that aren’t working—those changes should come in good or bad times. Rather, we can get so caught up in trying to reduce costs and increase sales that we forget the basics.
The management of a company’s waste stream is an example of a behind-the-scenes activity that should not be a major drain on profitability. With proper management waste treatment can result in such positives as reducing new lubricant purchases, lowering the cost of waste treatment, improving the environment and eliminating fines and a negative societal image. You also can generate sales of certain wastes as boiler fuel. In other words, a business case can and should be made for proper waste management and recycling—even in tough times.
All this sounds good, but there are a few key tenets of such a program:
1. A proactive maintenance program must be in place and reasonably well executed.
2. A top/down commitment must be made to reducing waste and pollutants, conserving resources and recycling materials at every stage of the product life cycle with the objective of improving the environment and reducing costs at each of these stages.
3. Whether they’re new, refurbished or recycled, use only lubricants and metalworking fluids that meet the specifications for their intended applications. This can never be compromised.
4. Recycling only makes sense when a global business case can be made for it.
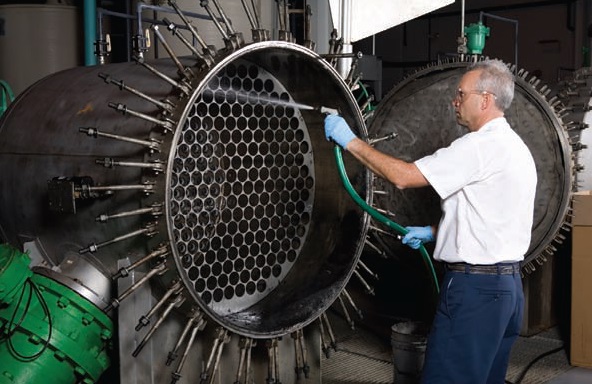
I hope it is clear that a global approach to manufacturing is needed for success, not just as it affects one department or another. Rather than compromising product quality, machine/tool life, manufacturing productivity and the environment, your objective is to maximize each of these in concert, globally. Whether direct or indirect, all these can be measured financially—the overall system must reduce total cost per unit manufactured to achieve maximum profitability. All that is fine, well and good, but sooner or later you must send your spent and unrecoverable fluids to the waste treatment plant. There are a few companies, GM in particular, that claim a number of their plants have reduced their industrial wastes to only that of sewage and cafeteria wastes.
While listening to STLE-member John Burke of Houghton International present the Waste Management portion of STLE’s Metalworking Fluids Certificate course, I was struck by another indirect factor impacting the cost of waste management. This has to do with managing the chemistries of the fluids and additives used in our processes to minimize the impact on waste treatment systems. The idea here is that if there are two chemicals that will do a given job—let’s say two antifoam agents—which of the two has the least negative impact on the waste treatment plant as well as the least value-in-use (cost/dose matrix).
Some of the key chemistries that impact the efficiency of the waste treatment plants include:
• Emulsifiers that stabilize oil-soluble additives in water-dilutable metalworking fluids by reducing interfacial tension between incompatible components by forming micelles (a submicroscopic aggregation of molecules, as a droplet in a colloidal system). These droplets then can remain suspended in the fluid. This is what you do when you wash your hands. Milk is an emulsion. In metalworking fluids, examples of emulsifiers are sodium petroleum sulfonate and alkanolamine salts of fatty acids.
• Couplers that assist in stabilizing water-dilutable metalworking fluids in the concentrate to prevent separation of components. Couplers facilitate formation of emulsions for soluble oils. Examples are nonionic additives like propylene glycol, glycol ethers and nonionic alkoxylates.
• Chelating agents (also known as water softeners or conditioners) reduce the destabilizing effect of hard water (calcium and magnesium ions) on metalworking fluid emulsions. Chelating agents bind calcium and magnesium salts (as well as other metal salts) to prevent them from reacting with anionic emulsifiers such as fatty acid salts of alkanolamines. An example might be ethylenediaminetetracetic acid.
One of the more common and cost-effective waste treatment systems is chemical treatment. This involves separating waste oil from water through chemical additions to achieve precipitation, flocculation and settling, or flotation, of oil-containing wastes. These wastes then are removed by filtration or by drawing off the concentrate from either the bottom or the surface, depending on the nature of the waste.
All too many plant operations people are not particularly aware of the issues affecting the operation of the waste treatment plant. This is especially the case when multiple waste streams from a wide variety of operations are dumped into a common treatment system. Thus, a well-meaning operations manager can inadvertently cause the waste treatment plant manager major problems and add significant cost to the overall operation of the plant.
In chemical treatment of waste, we are basically reversing everything we have done to stabilize the fluids we use—this is a key concept. In metalworking fluids, we carefully control pH around 9.0 to keep the fluid stable. At the waste treatment plant, we add acid to reduce the pH and make it unstable. (As we said earlier, milk is an emulsion. Add vinegar, lemon juice or another edible source of acid and you get buttermilk—and this is precisely the same operation as is run in the waste treatment plant.)
In addition, we add chemicals like aluminum sulfate, polyaluminum chloride, calcium chloride, magnesium sulfate, ferric chloride and ferrous sulfate. Most of these positive ions are the same ions encountered in metalworking operations; we add more of them to overpower the emulsifiers and reduce the stability of the fluids separating out the emulsified materials.
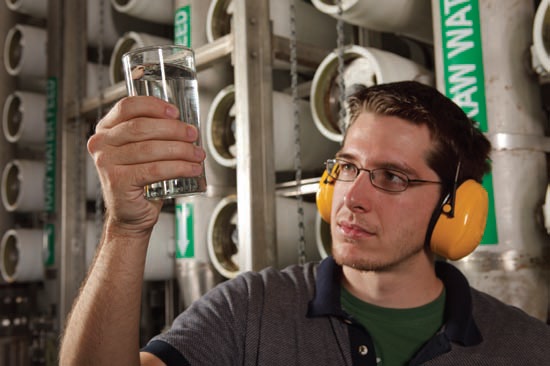
Nonionic emulsifiers don’t respond significantly to changes in pH. While that’s great for the operations, it causes chaos at the waste treatment plant. Couplers are essentially nonionic emulsifiers, and chelating agents reduce the destabilizing effects of hard water ions like calcium, magnesium, etc., which we just added at the waste treatment plant expressly for the purpose of destabilizing the waste stream.
Thus, to the extent that we can minimize these types of chemicals in the fluids as purchased, or minimize as additives used at the tankside to maintain the fluid life, we reduce the load on the waste treatment plant and thereby reduce cost. Clearly, all this is a balancing act. The more stable the fluid during its use, the longer it lasts and the less frequently we send it to the waste plant.
On the other hand, if the fluid is so stable that we can’t treat it without resorting to extreme measures, the money we saved in the operations is consumed in the waste treatment plant, possibly for an overall net loss. Probably the simplest, most cost-effective thing we can do in the plant is use only very good quality water. If the quantity of deleterious ions in the water is low, then we don’t need the quantities of additives (and labor) to overpower them, and, with fewer additives, the treatment plant costs less to operate.
Obviously, there are no simple quick-fix answers to these issues. Clearly, water quality, fluid selection and fluid management are linked to the final end result—success in waste treatment. The only real solution is for operations managers and the waste treatment manager to work together with their fluids suppliers to make the best overall compromises to minimize costs and maximize productivity—or, as we said above, the overall manufacturing system must reduce total cost per unit manufactured to achieve maximum profitability—globally.
Make time to discuss these concepts with the key people involved in your operations. In tough times, besides travel restrictions, layoffs, beating up your vendors and all the other draconian parts of today’s massive cost-cutting programs, focus and attention to the basics, like waste treatment, is all part of keeping your eye on the ball.
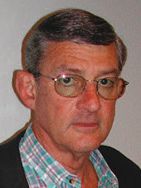
Bob Gresham is STLE’s director of professional development. You can reach him at rgresham@stle.org.