Aerospace Lubricants: Solid is essential in every sense
Jean Van Rensselar, Contributing Editor | TLT Feature Article June 2009
For planes and spacecraft that must battle vacuum conditions, radiation and extreme temperatures, solid lubricants provide the best solution.
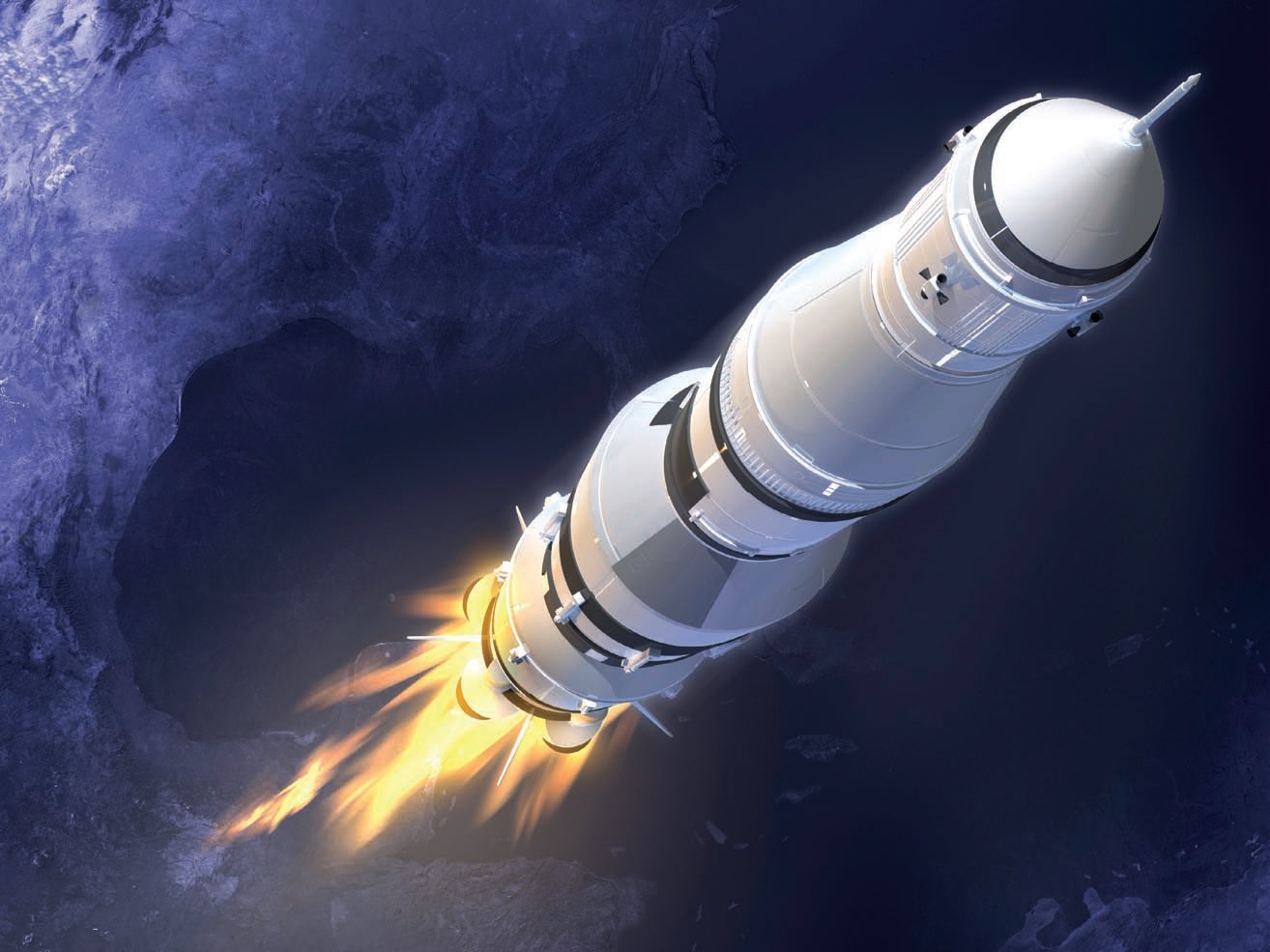
www.canstockphoto.com
KEY CONCEPTS
•
Once they leave the earth, planes and spacecraft can’t be serviced easily, which means lubricants must be reliable.
•
Solid lubricants compensate for conditions in space such as a vacuum atmosphere, radiation and extreme temperatures.
•
New technologies such as diamond-like carbon coatings and materials that can withstand extremely high temperatures are being tested.
Imagine you’ve just bought a new state-of-the-art hybrid car and are breaking it in with a long road trip. You’ve docked your iPod and are about 200 miles from the nearest town. You’re happily singing along to “Greased Lightning” …
Go greased lightning you’re burning up the quarter mile…when you hear CLUNK. Hmm, you probably hit a small pothole, you think, and continue on your way.
Go greased lightning you’re coasting through the heat lap trials. Greased lightning, go grease…CLUNK…CLUNK CLUNK…CLUNK CLUNK CLUNK…clunk…sssssssss.
The dashboard lights up like a prison yard, and your car slows to a halt somewhere between Out in the Middle of Nowhere and Is This Even on the Map? You try starting the engine again but realize it’s useless. Inconvenient—heck, yeah—but the worst part is that there’s no hope of repair ever, and you’ll have to abandon your new $45,000 investment.
Of course, this nightmare would never actually happen in the car world, which is filled with dealerships, expert mechanics and replacement parts. In the car world, the worse case scenario is a tow truck and a night or two in picturesque Coon River Falls.
But this is exactly what can happen in the aerospace world where it’s too late to make repairs once the machinery leaves the earth. It can happen with satellites priced between $100 million and $1 billion and a Boeing 747, a 400-passenger plane that runs anywhere from $198 million to $227 million (depending on the options). In addition, the Federal Aviation Administration figures that one Boeing 747 accident that destroys the plane mid-flight costs the airline about $1.3 billion, which explains why companies that own airplanes and spacecraft are not in an experimental mindset—especially when it comes to critical aspects like lubricants (
1).
“Aerospace customers tend to be very, very slow to accept new technologies,” explains Dr. Jeffrey Lince, senior scientist for The Aerospace Corp., headquartered in El Segundo, Calif. “Our customers purchase and operate satellites and interplanetary probes and launch vehicles. On earth if someone is having a lubrication problem with a crankshaft on a car or a piece of equipment on a factory floor, he can get it fixed fairly easily.
“With a satellite, once it’s launched, it’s gone,” Lince adds. “It’s extremely difficult, if not impossible to repair it. The sheer expense of these devices highlights why customers are so nervous about incorporating new technologies and why they don’t want to experiment with new lubricants.”
Lubricants that work well in terrestrial applications don’t always work well in aerospace applications for a number of reasons that include temperature extremes and different atmospheres.
But four decades of painstaking experimentation, observation and tribological simulation testing have produced lubricants that are effective and perform well under these demanding conditions.
Lince said his customers like the “tried and true,” which would mean solid lubricants that include molybdenum disulfide (MoS
2); polytetrafluoroethylene (PTFE), commonly known as Teflon®; and soft metals such as lead, gold and silver. These solid lubricants possess a number of unique properties that make them perfect for a wide range of aerospace applications.
Researchers are currently working on a number of promising new solid lubricant technologies geared for the aerospace industry. Other terms commonly used for solid lubricants include dry lubricants, solid-film lubricants and dry-film lubricants.
UNIQUE DEMANDS
Just how unique are aerospace lubricant demands? STLE-member Dr. W. Gregory Sawyer, N.C. Ebaugh professor at The University of Florida’s Department of Mechanical and Aerospace Engineering in Gainesville, Fla., plans to find out.
Sawyer and his team took four tribometers with lubricants, as shown in Figure 1, and mounted them on an active Materials International Space Station Experimental platform. Beginning in 2009, the platform and tribometers are scheduled to operate over one year in low earth orbit.
Figure 1. Four tribometers like this one have been mounted on an active Materials International Space Station Experimental (MISSE) platform. Beginning in 2009, the platform and tribometers will operate in low earth orbit for a year. (Courtesy of The University of Florida).
In space, the tribometers and solid lubricant samples will be exposed to the harsh environment of low earth orbit that includes radiation, ultraviolet light and atomic oxygen.
A total of eight tribometers designed and built at the University of Florida will be on this mission (four on the ram side and four on the wake). This is a joint and collaborative project with the tribology group at the Air Force Research Laboratory in Dayton, Ohio, which designed and built the four computers that will record and send data back during the mission.
In many cases, solid lubricants are easier to apply and less expensive to buy and maintain than their liquid counterparts. For many conditions—ranging from temperature extremes to radiation—solid lubricants perform better than liquid or gas films. Operating conditions in which solid lubricants excel involve:
•
Extremely high temperatures: Liquid lubricants can decompose or oxidize. The right solid lubricant can extend the operating temperatures of systems while maintaining relatively low coefficients of friction.
•
Cryogenic temperatures (below -150 C or 123 K): Liquid lubricants can solidify or become highly viscous and ineffective. The right solid lubricant can reduce the operating temperatures of systems down to -273.15 C (0 K).
•
Extreme pressure: In high to ultra-high vacuum conditions such as space—specifically a vacuum of ~10
-2 Pa or higher or a gas density of ~10
-12 molecules/cm
3 or lower at 24.85C (298 K)—lubricants can become volatile and also can evaporate and contaminate devices such as optical and electronic equipment.
•
High dust: Liquid lubricants tend to pick up dust—forming a grinding paste and damaging equipment—while solid lubricants do not.
•
Weight limitations: Since solid lubrication weighs less than liquid, it’s ideal for spacecraft maneuverability and also extends mission length.
•
Corrosive environments: When equipment is stored or idle for long periods, solid lubricants remain stable.
•
Radiation: Liquid lubricants tend to decompose in the presence of radiation. The right solid lubricant can extend system operations beyond 106 rads—the same as an absorbed radiation dose of 10
4 J/kg—while maintaining relatively low coefficients of friction.
For a general overview, see sidebar,
“Advantages and Disadvantages of Solid Lubricants.”
Advantages/disadvantages of solid lubricants
Advantages
•
Very stable in high-temperature, cryogenic, vacuum and high-pressure environments
•
High heat dissipation (with high thermally conductive lubricants)
•
High resistance to deterioration in the presence of radiation
•
High resistance to abrasion in the presence of dust
•
High resistance to deterioration in corrosive environments
•
More effective than fluids at high loads and high-speeds
•
High resistance to deterioration in storage
•
Lighter and less complex equipment—lubrication distribution systems and seals are not required
•
Reliability—for applications where servicing is difficult or impossible.
Disadvantages
•
Have higher coefficients of friction and wear than liquid lubricants
•
Have poor heat dissipation with low thermally conductive lubricants such as polymer-based films
•
Have poor self-healing properties—a broken solid film may shorten the lubricant life
•
May have an undesirable color (i.e., graphite).
Dr. Chris Muratore, a visiting scientist at The Air Force Research Laboratory in Dayton, Ohio, has developed cutting-edge materials designed to lubricate from 25 C (298 K) to 700 C (973 K). While many materials can provide lower friction coefficients, Muratore’s materials are among the very few that can lubricate over that entire temperature range.
“We’ve developed nanocomposite solid lubricant coatings for this temperature range with friction coefficients of 0.2 or less and wear rates that are lower than many solid lubricants intended for much narrower temperature ranges,” Muratore explains. “These composite materials employ several different adaptive mechanisms that operate within different ranges bounded by those temperature limits to yield such low friction coefficients, which are the lowest we know of for any multi-temperature lubricant.”
PROPERTIES & AEROSPACE APPLICATIONS
Several properties determine the feasibility of using a material as a solid lubricant for the aerospace industry:
•
Thermal stability: One of the most important solid lubrication aerospace applications is in extremely high- or low-temperature environments. Good thermal stability ensures that the solid lubricant will not undergo negative phase or structural changes at temperature extremes.
•
Oxidation stability: The lubricant should not undergo negative oxidative changes when used in air and within the material’s temperature range.
•
Volatility: Low vapor pressure is essential because of extreme temperatures and the need to avoid contamination in or under low-pressure conditions.
•
Chemical reactivity: The lubricant should be able to form a strong, adherent film on the base material.
•
High melting point: When the melting point is exceeded, the atomic bonds that maintain the molecular structure are ruined, making the lubricant ineffective.
•
Crystal structure: Solid lamellar-structure lubricants such as graphite and MoS
2 have an inherently low shear strength and are generally preferred over non-lamellar lubricants.
•
Optimal hardness: A maximum hardness of 5 on the Mohs scale is the practical limit for solid lubricants.
•
Electrical conductivity: The degree of the material’s conductivity must be matched to the application. For instance, insulators making rubber contact require low conductivity while sliding electrical contacts require high conductivity.
Dr. Jeffrey Lince prepares to make pin-on-disk friction and wear measurements. This testing is performed to measure the sliding coefficient of friction between two materials under ambient or purged atmospheres. (Courtesy of The Aerospace Corp.)
The following table (
see below) lists properties of solid lubricants and the aerospace applications that demand those properties (
2).
Solid film lubricants protect better than most mineral and synthetic oil-based fluids. They also have upper temperature ranges well above fluids.
“With space, there are a number of design hurdles,” says Lince. “Liquid lubricants are used a lot in spacecraft for a number of applications, but they are very limited when you have temperature extremes. Solid lubricants tend to retain their properties over a wide temperature range.
“Liquid lubricants migrate to neighboring devices, but solid lubricants tend to stay where you put them,” he adds. “It’s also a lot easier to apply and handle solid lubricants. Aside from these, there are a number of minor properties that make solid lubricants more attractive for aerospace applications.”
WIDELY USED MATERIALS
The four most common solid lubricant classes are MoS
2, graphite, PTFE and soft metals. Crystalline lattice (lamella) structure materials—such as MoS
2, graphite and tungsten disulfide—are both lubricant agents and stand-alone lubricants. They’re used independently or combined with metals such as lead, copper, silver and gold. These lamella-lubricating powders are especially appealing because they have low shear forces between their crystalline lattice layers, which minimize sliding surface resistance. Long-chain fluorocarbon molecules such as PTFE have wetting angles that promote release. They also have characteristics that make them ideal for high-temperatures.
“Speaking as a tribologist in the space business, I know we have a tendency to stick with materials we’re familiar with, so we are beating materials like MoS
2 to death,” Lince said. “Generally, there is a small handful of solid lubricants that we use in space. They are transition metal sulfides like MoS
2, Teflon and then soft metals like gold. They work because they’re all relatively easy to smear—they have low shear strength. Also, they are very chemically inert and don’t stick to contacting surfaces, which is important to achieve good lubricating characteristics.”
Let’s examine the four classes in greater detail and also look at a few other materials.
Molybdenum Disulfide. Although it’s predominant mineral, molybdenite, was used in the 1300s, molybdenum was not positively identified until 1778 and wasn’t commercialized until the technology for mineral extraction was developed 100 years later. Molybdenum does not occur naturally in its metallic form, but MoS
2 occurs naturally as thin, solid veins in graphite and must be highly refined for use in solid lubricants.
MoS
2 has a hexagonal crystalline structure with a natural easy shear that occurs at the interface between the sulfur molecules (
see Figure 2). Because there is no vapor between lattice plates, MoS
2 is effective in high-vacuum conditions where graphite will not work, hence its lubrication capacity often exceeds that of graphite.
Figure 2. Molecular structure of Molybdenum Disulfide (MoS2) (Courtesy of Dynamic Coatings Inc., www.DynamicCoatingsInc.com)
MoS
2 has a low coefficient of friction in both vacuum and atmosphere. It doesn’t rely on adsorbed vapors or moisture. Its thermal stability in non-oxidizing environments reaches 1373 K, but in air its use is limited by oxidation to anywhere from 349.85 C (623 K) to 399.85 C (673 K).
MoS
2 has a greater load-carrying capacity than either graphite and PTFE.
Graphite. Graphite, a soft crystalline form of carbon, occurs naturally in metamorphic rocks such as marble and gneiss and exhibits the properties of both a metal and nonmetal, making it desirable for many applications. Its metallic properties make it a good thermal and electrical conductor, and its nonmetallic properties include stability, lubricity and high thermal resistance.
Graphite has a layer lattice lamella crystal structure with bonds between the carbon atoms within the layers that are stronger than the carbon bonds between the layers. The benzene ring structure has layered plates that are not covalently connected to the surrounding layers (
see Figure 3).
Figure 3. Molecular structure of graphite (Courtesy of Dynamic Coatings Inc., www.DynamicCoatingsInc.com)
Graphite has a low coefficient of friction and very high thermal stability, 2273 K and above. It has the easy shear of MoS
2 but relies on adsorbed moisture or water vapor to achieve low friction, so its value in dry environments such as high altitudes and space is limited. With a moisture vapor barrier, graphite will lubricate up to about 1,450 F, and because it requires an entrained moisture vapor it doesn’t lubricate well in a hard vacuum, making it less than ideal for deep-space equipment. Because of oxidation, the practical temperature application ranges from 499.85 C (773 K) to 599. 85 C (873 K).
PTFE. In 1938 Dr. Roy Plunkett accidentally discovered PTFE at DuPont’s Jackson Laboratory in Deepwater, N.J. Plunkett was working with chlorofluorocarbons and, while checking a frozen compressed sample of tetrafluoroethylene, discovered that the sample had spontaneously polymerized into white waxy PTFE, later named Teflon.
Because it lacks chemical reactivity, it has a low coefficient of friction (as low as 0.04) in both vacuum and atmosphere. It doesn’t rely on adsorbed vapors or moisture and possesses low surface energy. Practical application temperatures range from -100.15 C (173 K) to 299.85 C (573 K). PTFE’s low thermal conductivity inhibits heat dissipation, which causes melting and premature failure. This limits its use as a substitute for MoS
2 in low-speed sliding applications.
PTFE is a saturated aliphatic fluorocarbon that does not have the mechanical occlusion characteristics of graphite or molybdenum. Surfaces coated with it resist wetting, and it is unaffected by acids, bases or solvents at temperatures less than 260 C (533 K). PTFE is inert to virtually all chemicals and is the most slippery material in existence.
Fillers are added to PTFE to enhance characteristics. For example, glass fiber promotes high wear resistance and low friction, and graphite promotes chemical and creep resistance.
PTFE is an excellent lubricant at low loads but fails at higher loads.
Atomic-scale structure that develops when a solid lubricant containing MoS2 undergoes sliding contact with the microscope probe tip. (Courtesy of The Aerospace Corp.)
Soft Metals. Soft metals used as lubricants include lead, gold, silver, copper and indium. They possess relatively low coefficients of friction, both in vacuum and atmosphere. These metals are extremely useful for high-temperature applications up to 999.85 C (1273 K) and for rolling element applications such as roller bearings.
Other materials. Boron nitride is a ceramic powder lubricant with an impressive high temperature resistance of 1,200 C (1473 K) in an oxidizing atmosphere. It also has a high thermal conductivity.
Tungsten disulfide (WS
2) has a coefficient of friction of 0. 03-0.1 in humid air from 25 C to 400 C (273 K-673 K) and offers excellent dry lubricity. It also can be used in high-temperature and high-pressure applications. MoS
2 is generally a better solid lubricant than WS
2 in vacuum, but WS
2 beats MoS
2 in higher temperature air environments. WS
2 is more expensive than MoS
2 and graphite.
Other solid film lubricants include talc, calcium fluoride and cerium fluoride.
Composites. MoS
2, graphite, PTFE and other antifriction and antiwear additives are often compounded in polymers and a variety of sintered materials. MoS
2 compounds, for example, are used in materials for sleeve bearings, elastomer O-rings and carbon brushes. Solid lubricants are compounded in plastics to form self-lubricating (internally lubricated) thermoplastic composites, which are often used in ball bearing retainers. Composites also can be formed in thin coatings, improving their tribological properties.
Lince has formulated gold-doped MoS
2 coatings that enhance existing solid lubricant applications and open the door for new applications.
“Lubricants, in general, are very non-conductive, so they don’t promote good sliding electrical contacts,” says Lince. “We’ve found that when we use high gold content in MoS
2 coatings, they can lubricate effectively at low contact stresses, which is beneficial because typical metal/MoS
2 coatings are used for high-contact stresses. Our coatings seem to work well in sliding electrical contacts and low contact stress applications—using high metal content expands the applications for MoS
2.”
Application Methods
Typical powdered solid lubricant application methods include:
•
Burnishing: A thin film of dry-powdered solid lubricant, such as graphite and MoS
2, is applied to a metal surface. This process produces a highly polished surface that is effective where lubrication requirements and wear life are not critical. It is also effective where there are clearance requirements and wear debris from the lubricant needs to be minimized.
•
Dispersion: A solid lubricant is mixed in a fluid lubricant and applied as a fluid lubricant.
•
Impingement: A solid lubricant is blasted under high air pressure onto a surface. This forms a more adherent, uniform coating than burnishing but should still only be used in non-critical applications.
•
Bonding: A resin or inorganic binder in liquid form is mixed with a solid lubricant powder. The part is coated by spraying or brushing the liquid on the surface, followed by air or heat curing to form an adherent coating. This is used widely in aerospace applications.
•
Sputtering: The solid lubricant is ion-sputtered, usually in a vacuum chamber with the use of a plasma, causing lubricant material to be transferred to the part surface. The resultant coating is thinner, more adherent and generally has greater endurance than other types of solid lubricant coatings. However, it is more expensive and it is difficult to coat complicated part geometries. This technique is used in the most critical aerospace applications.
IN DEVELOPMENT
A number of new applications involving long-term life and operation across a broad temperature range have prompted renewed interest in solid lubricant research. These applications include lightweight moving mechanical assemblies and tribological components for long-term service in space mechanisms and cages for turbo pump bearings operating in liquid hydrogen and oxygen.
According to NASA, the following solid lubricant technologies now under development show promise (
3):
•
Carbon nanotubes (both single-walled and multi-walled)
•
Fluorinated carbon nano-onions
•
Multi-nanolayered composite coatings (MoS
2/WS
2/C and MoS
2/WS
2)
•
Functionally graded, multilayered inorganic coatings (TiC
x/C and TiC
x)
•
Multilayered composite coatings (WC/C, MoS
2/C, WS
2/C and TiC/C)
•
Nanocrystalline diamond coatings
•
Large-area diamond-like carbon coatings
•
TiO
2 grown on 55Ni-45Ti and titanium-based alloys
•
Ceramics and advanced coatings (BN, B
4C, VC, AIN, Cn
x, TiO
2, SiO
2, etc.)
•
Soft metal coatings and PTFE deposited with advanced techniques
Muratore is researching lubricating materials that can push current temperature limits.
“The thrust of our future efforts will be to expand the upper end of our current temperature limit of 750 C,” he says. “For higher temperature applications, we are considering several double-oxide compounds, which have a layered atomic structure with weak interplanar bonding similar to that observed in molybdenum disulfide but which can maintain their structure and composition at much higher temperatures.”
Muratore has been collaborating with other researchers such as Dr. Samir Aouadi, associate professor in the department of physics at Southern Illinois University in Carbondale, Ill., who has worked with The Air Force Research Laboratory (AFRL) to further advance adaptive coatings suitable for use in a broad temperature range. These coatings are composed of MoS
2 and silver with a reactively sputtered molybdenum nitride matrix.
“The coating materials that we’ve developed at AFRL have typically involved at least one component that has to be deposited via pulsed laser deposition, because it’s an electrically insulating oxide compound,” says Muratore. “It’s difficult to scale-up laser deposition processes for industrial production, which has motivated our work with Samir at SIU to study materials that can be deposited strictly via magnetron sputtering—a process widely accepted by industry.”
Muratore is also working with a coating manufacturer to produce coatings for high-mach-number flights and has had several informal discussions with high-performance automotive engine and heavy machinery manufacturers interested in his work, especially on adaptive coatings with built-in wear sensors.
His initial motivation for developing these innovative coatings came from studies of multilayered adaptive lubricant-diffusion-barrier-layer coatings designed to operate over multiple thermal cycles.
“We wanted to have an understanding of how the multilayered coatings wore over a single high-to-low thermal cycle, since materials that are lubricous at high temperatures are often abrasive at low temperatures,” he says. “Initial results from those studies suggested that each adaptive layer lasts through one phase of the thermal cycle. Therefore, two thermal cycles require a coating of at least four adaptive solid lubricants layers and so on. This is a valuable insight as we go forward to try to expand the number of thermal cycles adaptive tribological coatings can endure.”
In addition, Muratore realized the value of smart coatings that can report the extent of wear while in use. These coatings have been recognized as an extremely useful innovation for machine tools, but they may be especially valuable for bearings in expensive aircraft engines operating at high-mach speeds.
“I anticipate that the savings of time and money would be substantial in both the aerospace and tool cases,” he says. “In a broader sense, I think a reliable, integrated sensor system allows both engineers and ultimately operators to push the limits of coated components, where they may have been reluctant to do so without a failure warning mechanism. The sensors are necessary to truly maximize the benefits of coating materials.”
Muratore believes that while embedded wear sensors will eventually be incorporated into future aerospace applications, it’s still some time away.
“Based on the response from the public, the interest in the sensor concept is high for tools, high-performance auto engines and heavy machinery,” he said. “These are things that will not fall out of the sky if prototype wear sensors have bugs that need to be worked out.”
One of Lince’s focuses is highly hydrogenated diamondlike carbon (DLC).
“Normal diamond-like carbon, with lower levels of hydrogenation, doesn’t perform that well in a vacuum,” he says. “It generally needs a little bit of moisture. So they are used in many, many terrestrial applications such as piston rings. But for space, you need a coating that performs well in vacuum, where these highly hydrogenated DLC coatings seem to work well. They have a very low friction coefficient and a relatively high shear strength. They have the dual advantages of being hard coatings and having low friction in a vacuum—in contrast to most solid lubricants, which have low shear strength.”
Lince is also working the nanoparticles. MoS
2 nanoparticles overcome some of the inherent weaknesses of the material.
“MoS
2 has some moisture sensitivity,” he explains. “So if it comes in contact with air, it can oxidize. The situation can be solved with the use of nanoparticles, which form a closed structure and don’t allow the moisture and oxygen in the air to attack the MoS
2 structure.”
STLE-member Dr. Kathryn Wahl, head of the Molecular Interfaces and Tribology section at The U.S. Naval Research Laboratory (NRL) in Washington, D.C., and her colleague, Dr. Irwin Singer, have pioneered work on in situ Raman tribometry of solid lubricants.
The study of low-friction, solid-lubricated interfaces requires approaches that evaluate and describe near-surface properties.
According to Wahl, these interfaces are challenging to study because much of what controls friction and wear occurs in “buried” interfaces that are both chemically and mechanically inaccessible to normal experimental approaches.
One solution to this dilemma is to replace at least one of the sliding counterbodies with a transparent material such as glass, sapphire or mica. Since most solid lubricant coatings are not transparent to visible light wavelengths, Wahl’s team chose to use a transparent hemisphere as a counterbody to allow visualization of the contact.
Photograph of a smart coating testing system that automatically reports remaining wear life of solid lubricant coatings (shown on the left) via laser interrogation of the coating with embedded sensor layers (schematically, shown on the right) known to produce very bright and distinctive luminescence spectra when illuminated. (Courtesy of The Air Force Research Laboratory)
She explains, “We set up our first in situ tribometer at NRL using a homebuilt reciprocating stage with a force sensor under the coating sample and a rigid, dead-loaded counterbody consisting of a half hemisphere placed under a microscope objective. The microscope could be operated either for white-light-illuminated videography of the sliding contact or as a micro-Raman system focused to a spot inside the contact.
“The first experiments we performed were very enlightening, as we immediately saw, in real-time, interfacial ‘transfer film’ formation, along with the concomitant friction reduction,” Wahl continues. “We also observed that the interfacial films were typically relatively stationary, except when friction was high, and we were even able to play back video to observe the nucleation of damage to a wear track that had later resulted in localized coating failure and high friction.”
Wahl and her team performed Raman microscopy on the transfer films and wear tracks through the contact. Later, using spectroscopic and interferometric methods, they were able to conduct a more detailed analysis including a thickness estimate of transfer films.
Applied together, these methods enabled the NRL team to develop a better, though not complete, picture of the events happening in the buried interface during sliding. They were able to observe the following:
•
Which materials transferred
•
Where the sliding interface occurred
•
How much motion occurred within the interface
•
Morphology changes
•
Wear and plowing events that resulted in friction spiking and instabilities.
Wahl says, “While the observations are only on an optical microscopy size scale—at best about one micron lateral resolution—in situ methods such as these provide a powerful method to take some of the guesswork or speculation out of interpreting a wide range of friction behavior in solid-lubricated contacts.”
Lince is exploring DLC as both a stand-alone lubricant and an additive for lubricating bearings.
“One of the problems with liquid-lubricated bearings is that generally, when they fail, they fail because of chemical degradation of the liquid lubricant,” he said. “In an all-steel ball bearing, the ball is constantly rolling against the steel race in the presence of a lubricant. The lubricant degrades due to chemical reaction with the steel at the metal-to-metal contact. But if you apply DLC to one or both of the surfaces, we’ve found that the chemical degradation is greatly reduced.”
TECHNOLOGY FOR EVERYONE
While aerospace companies may be hesitant to incorporate new technologies, at some point they must—basically when the old technology stops working.
“The threshold of proof for us is very high, much higher than for terrestrial lubricants,” Lince says. “Typical diamond-like carbon coatings with low hydrogen contents already have been explored for use in space hardware. But, predictably, problems are occurring because they are using a technology that has been effective in terrestrial applications and are applying it to the vacuum environment in space.
“It’s been a challenge,” he adds. “Failures with misapplied materials make it harder for folks in the space business to accept similar but more appropriate materials like the highly hydrogenated DLC, which should work better in space applications.”
The technology of solid lubrication has advanced rapidly in the past four decades, but the continued exploration of the moon and Mars and the success of extraterrestrial habitats and vehicles are critically dependent on the correct and reliable operation of moving mechanical assemblies and tribological components.
Solid lubricants fill the void left by liquid lubricants that do not meet the advanced requirements of aerospace, such as vacuum conditions, high temperatures, cryogenic temperatures, radiation, dust or corrosive environments.
Mars is, in essence, the perfect storm of all these conditions: the vacuum of space, extreme daily temperature swings, cosmic radiation, a corrosive atmosphere and dust. But one or more of these conditions exists everywhere to some extent. Nearly every manufacturing plant has operating conditions that could be considered extreme from a lubrication perspective: high pressure, high and low temperatures, corrosive contaminants and/or dust.
While the development of cutting-edge solid lubricants will have positive implications for aerospace, many other industries will benefit as well.
•
What if industrial machinery never broke down or what if it warned operators before it did?
•
What if aircraft lubrication never failed and accidents were reduced?
•
What if solid lubricants could extend the life of space equipment nearly forever?
•
What if your new hybrid car lasted past the opening bars of “Greased Lighting” and six more decades on top of that?
Wahl says, “On a personal note, I have found that every coating we have ever examined provided a different, new contribution to our understanding of solid lubrication phenomena. It has been a rich experience for me as a tribologist to have the opportunity to study solid lubricants in this way.”
REFERENCES
1.
Initial Regulatory Evaluation, Initial Regulatory Flexibility Determination, Initial International Trade Impact Assessment, and Initial Unfunded Mandate Assessment for Proposed Rule: Fuel Tank Flammability Reduction: Airbus and Boeing Airplane Fleets, CFR Parts 25, 19, 121, and 129. Office of Aviation Policy and Plans. Aircraft Regulatory Analysis Branch. Allen A. Mattes. Nov. 2005.
2.
Miyoshi, K.,
Solid Lubricants and Coatings for Extreme Environments: State-of-the-Art Survey, Glenn Research Center, Cleveland, Ohio, Jan. 2007.
3.
Ibid.
Jean Van Rensselar heads her own communications firm, Smart PR Communications, in Naperville, Ill. You can contact her at Jean@SmartPRcommunications.com.