Heat Transfer Fluids: Selection, maintenance & new applications
Dr. Neil Canter, Contributing Editor | TLT Cover Story May 2009
As the need for energy conservation increases, the importance of these fluids continues to grow.
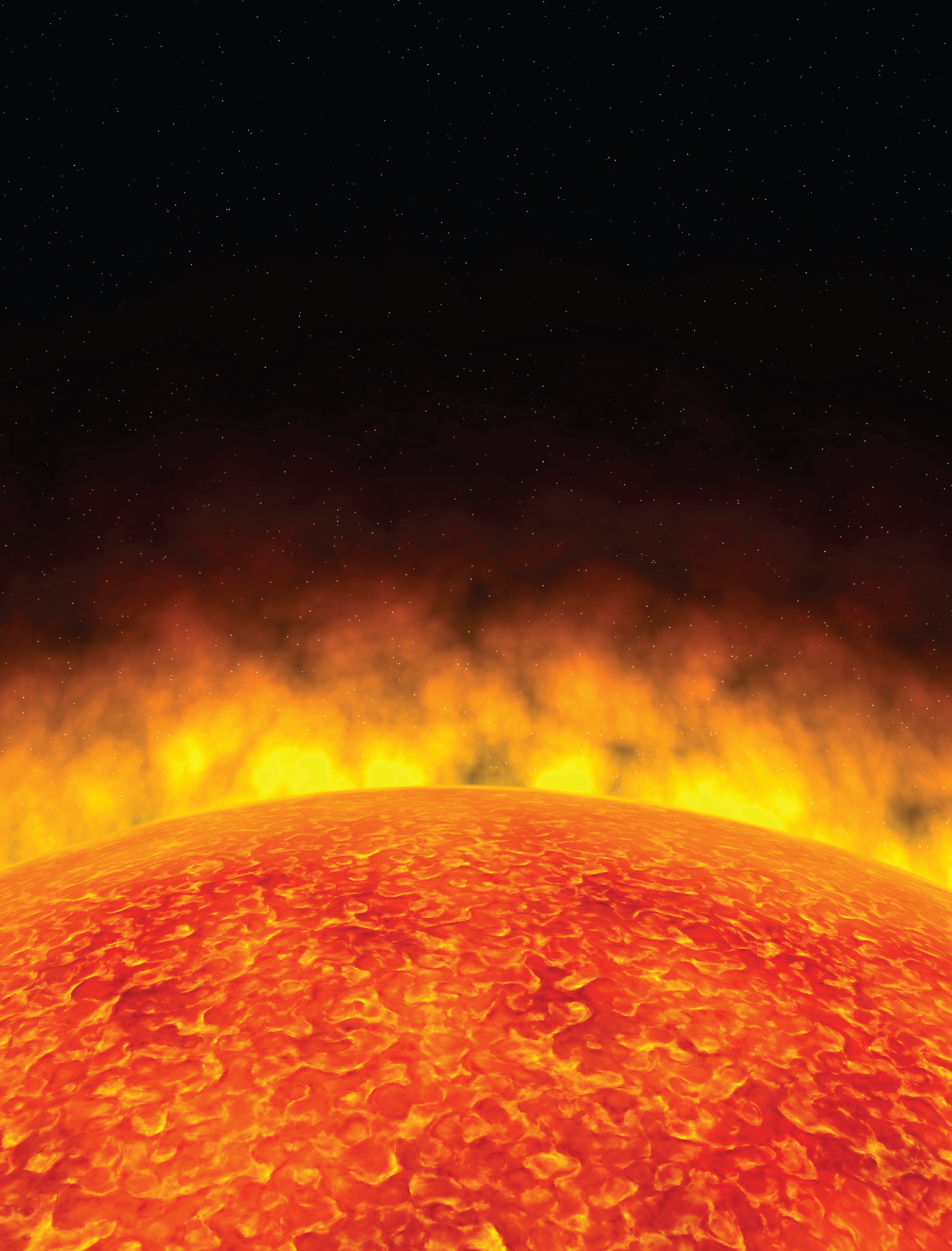
www.canstockphoto.com
KEY CONCEPTS
•
Heat transfer fluids serve an important role in the efficient use of energy.
•
A number of criteria must be examined before recommending a heat transfer fluid. Selection is important because heat transfer fluids can last more than 10 years.
•
New applications for heat transfer fluids that show promise are in solar power, geothermal energy, natural gas compressors and secondary loop refrigeration.
•
Work continues to incorporate nanoparticles in heat transfer fluids because of the potential for enhanced thermal conductivity.
Management of heat in industrial and residential applications is becoming more important as we strive to improve the efficient use of energy. Heat transfer fluids have been an integral part of this process for many years. The importance of heat transfer was noted by the Romans, who designed hot-air distribution systems for heating homes and public baths (
1).
Heat transfer fluid suppliers have developed a variety of organic- and water-based fluids to meet the operating needs of diverse applications. Among the former are petroleum and synthetic fluids derived from mineral oils, white/paraffinic oils, synthetic aromatics (such as poly phenyls and alkylated benzenes), silicones and fluorocarbons. Water-based heat transfer fluids are formulated primarily with ethylene glycol and propylene glycol.
This article reviews the criteria used to select and maintain heat transfer fluids, highlights new applications such as solar power and discusses the development of nanoparticle-containing heat transfer fluids.
SELECTION CRITERIA
Dr. Satish Mohapatra, president and CEO of Dynalene Inc., in Whitehall, Pa., strongly believes that the key fluid property that must be ascertained in the selection process is its temperature range. He says, “Determination of the temperature range is extremely important. There is no point in discussing other fluid characteristics until the temperature range is satisfied. Once this criterion is fulfilled, other important fluid properties (i.e., viscosity, density, specific heat and thermal conductivity) can be considered.”
The various types of heat transfer fluids can create specific problems in systems. Mohapatra says, “Before examining the actual application, the customer must evaluate the compatibility, cost, environmental impact and toxicity of the heat transfer fluid. In petroleum and synthetic hydrocarbon-based heat transfer fluids, incompatibilities can be found with commonly used seals and gaskets such as EPDM (ethylene propylene diene M-class) rubber and silicone.”
“End-users must decide whether they need to use Teflon, Viton, graphite or even a metal gasket depending on the highest temperature of the application. With water-based glycol fluids, corrosion can be a major issue, particularly if different metals are involved in the system. The temperature at which the system operates also can affect the rate of corrosion.”
For Michael Bates, technical director of Duratherm Extended Life Fluids in Lewistown, N.Y., different customers have different needs which dictate the selection of the heat transfer fluid. He adds, “A number of criteria such as heat capacity and thermal conductivity must be evaluated, but the key parameters are determined by such factors as the size of the system, heating source (gas fire boiler, electric resistance heaters), pumping capabilities and perhaps any flash point requirements of the fluid.”
The latter factor, flash point, can be an important consideration if the heat transfer boiler is located in close proximity to electrical utilities or other potential ignition sources. It can often be of concern to insurance companies, fire marshals and other regulators.
STLE-member Dr. Steve Stanley, global business director, Performance Fluids for The Dow Chemical Co., in Midland, Mich., indicates that the temperature range of the heat transfer fluid must be determined to ensure that the fluid is compatible with the application. He says, “Temperature range and not just the highest use temperature for a specific fluid type is very important. Viscosity and pumpability are important factors because both impact the economics of the operation. If the viscosity is too high, then a large amount of electricity could be consumed in pumping the fluid through the system.”
High temperature fluids operate at temperatures up to 400 C (752 F). Above 315 C (600 F), options are limited to synthetics. Below that temperature, mineral oil-based fluids are viable. Low temperature fluids are water-based and contain either ethylene glycol or propylene glycol. Operating temperatures for water-based fluids on the low end are down to -40 C. Synthetic fluids can operate at even lower temperatures. One synthetic hydrocarbon-based heat transfer fluid has an operating range down to -112 C (-170 F).
Conrad Gamble, technical service principal for Solutia, Inc., in St. Louis, Mo., lists specific heat, thermal conductivity, density and viscosity as important performance considerations. He says, “The key consideration is the efficiency at which the fluid can transfer heat away or toward a specific application. But the complexity of heat transfer applications means you cannot have tunnel vision by picking only one or two properties to the exclusion of other factors. Selection of a fluid having a maximum bulk temperature range marginally above the design operating temperature of the fluid can often significantly extend the fluid life.”
Different criteria need to be evaluated for high temperature and low temperature applications. In the former case, Budd Lee, development leader for the Performance Fluids Division of The Dow Chemical Co., says, “Initially, the question needs to be asked about whether the fluid operates in the liquid or vapor phase. Most current applications are in the liquid phase. Heat transfer coefficient is an important parameter but may need to be combined with durability. Silicon-based fluids are very durable but are not nearly as efficient from a heat transfer perspective as other organic-based fluid types.”
On the low temperature side, Kevin Connor, technical service specialist for The Dow Chemical Co., says, “Toxicity and environmental friendliness are two important criteria in low temperature applications because the choice is between fluids based on ethylene glycol and propylene glycol.”
Ethylene glycol has better heat transfer properties, including a higher density and lower viscosity, but propylene glycol is essentially non-toxic and more environmentally friendly. These parameters assume more importance in applications such as those found in the food industry.
‘While use of heat transfer fluids in solar power applications is relatively new as compared to industrial use, it has still been around for 20 years.’
FLUID MAINTENANCE
Heat transfer fluids are designed to last over a long operating time frame. Stanley says, “Most heat transfer fluids are formulated to operate for at least 10 years. The median lifetime is usually approximately 20 years. We have some fluids that have been in service for 30 years.”
For high-temperature applications, hydrocarbon and organic-based fluids are evaluated over time for solids content, water percentage and viscosity. Lee indicates that analysis of the fluid’s composition by the use of a gas chromatography (GC) simulated distillation is particularly useful. He adds, “If the concentration of high boilers increases above 10%, then it is time to change the heat transfer fluid. High boilers are formed through the combination of free radical species. Their higher level means fluid oxidation is readily occurring.”
Corrosion is a major factor in low temperature heat transfer fluids because they are water-based. Stanley says, “In doing fluid checks, careful analysis of corrosion inhibitors needs to be done to determine the extent of corrosion protection provided by the fluid. If insufficient, then the fluid may need to be supplemented with additional corrosion inhibitors.”
Heat transfer fluids need to be monitored on a periodic basis, according to Bates. In some applications, fluids can last upward of 10 to 15 years, but in many applications, due to system design, this could be as short as three to four months. It is therefore important that fluid analysis be employed on a regular basis at suitable intervals to ensure fluids are changed before they degrade.
Bates says, “No maintenance is typically required on heat transfer fluids, but regular analysis is very important.” In assessing the condition of a heat transfer fluid, Bates indicates that the changes in certain physical parameters can provide clues about why fluid performance is declining.
For example, Bates relates how a heat transfer fluid has been working fine for two to three years and then all of a sudden the total acid number (TAN) suddenly rises. TAN is the key indicator of oxidation. He explains, “A system expansion tank can play a critical role in ensuring fluids are not being oxidized during normal operation. In most cases, hot fluid is not flowing through the expansion during normal operation. However, for venting purposes most systems have the ability to flow hot fluid through the expansion tank for a short period of time, but in this particular case the customer left this open for an extended period of time and quickly oxidized the fluid.”
A second example involves the reduction in the flash point and viscosity of a heat transfer fluid. In this case, Bates indicates that the wrong pump was used to move fluid through a boiler. He says, “The result is that the fluid moved too slowly through the boiler and, as a consequence, picked up too much heat, leading to its decomposition.”
NEW APPLICATIONS: SOLAR POWER
Heat transfer fluids are used in a myriad of industrial and commercial applications. With the large increase in energy costs for traditional petroleum sources, options are being looked at to generate electric power. One approach is to utilize solar power.
Gamble says, “While use of heat transfer fluids in solar power applications is relatively new compared to industrial use, it has still been around for 20 years. In the mid-1980s, we were supporting development of solar power plants in the Mojave Desert in the southwestern U.S.”
Stanley indicates there are in fact three different approaches for utilizing solar power. He says, “Large solar systems are being built in different parts of the world. These systems are composed of parabolic-curved, trough-shaped reflectors that focus the sun’s energy at 30 to 60 times its normal intensity onto a receiver pipe containing a heat transfer fluid. The fluid is then used to generate steam, which powers a turbine through an electric generator.” Figure 1 shows a parabolic solar collector.
Figure 1. A parabolic solar collector focuses the sun’s energy onto a receiver pipe containing a heat transfer fluid to generate steam used to produce electricity. (Courtesy of Solutia Inc.)
The other two technologies are photovoltaic solar cells and individual solar heating systems that are placed on the roofs of homes and utilize propylene glycol or ethylene glycol-based heat transfer fluids to heat water.
Lee points out that the parabolic solar collectors utilize synthetic heat transfer fluids because temperatures can rise up to 400 C. He says, “We developed a fluid for use in a solar power plant that was started up in the state of Nevada in 2006. The initial charge required three million pounds of heat transfer fluid for the 64-megawatt plant.”
Other solar power plants are being built in Spain and Egypt. One other strategy to maximize the amount of solar power collected is using molten salts to store the energy so it can be used during the evening.
Gamble estimates that the proper heat transfer fluid can last for at least 20 years in some solar power applications. He says, “Long fluid life can be attained if the most stable organic-based synthetics are used. The heat transfer fluid industry is looking to work at higher temperatures above 400 C in the future. But the challenge for us is to determine how this would be possible.”
GEOTHERMAL ENERGY
In the search for alternative energy sources, more attention is being paid to the ground beneath housing as a source for heating and cooling. STLE-member Ken Lilje, director of R&D for CPI Engineering Services, in Midland, Mich., a subsidiary of The Lubrizol Corp., says, “The constant nature of underground conditions can be utilized to heat or cool a house using a heat transfer fluid depending upon whether it is summer or winter. The heat transfer fluid circulates down into the ground and in the summer dissipates heat from the environment to cool the house. In the winter, the process will reverse; the fluid transports heat from the ground into the house.”
This heat transfer is possible by burying a plastic pipe containing the heat transfer fluid in the ground. The pipe is connected to a heat pump/air conditioning unit and can go forward or in reverse depending upon the season.
The heat transfer fluids currently used are water-based due to low temperature range requirements. Lilje says, “Fluids based on methanol, ethanol, ethylene glycol and propylene glycol are commercially available.”
Heat transfer fluids used in geothermal energy applications must exhibit several key characteristics. Lilje says, “Low toxicity, non-flammability and good corrosion protection are very important because the fluid is being used in a residential setting.”
Lilje explains that the fluid types currently used have negative characteristics. He says, “Methanol and ethanol are volatile, flammable and toxic. Ethylene glycol is also toxic and is viscous at low temperatures. While environmentally friendly, propylene glycol is also viscous at low temperatures and can support microbial growth that could degrade the fluid and generate corrosion.”
Using the right heat transfer fluid is also important because operating life is expected to be at least 10 to 12 years. Lilje adds, “If the heat transfer fluid system is kept closed, properly maintained and the fluid is non-flammable, nontoxic and has a good environmental profile, then there is no limit to the operating life.”
An alternative product based on potassium formate has been introduced that provides improved thermal conductivity with non-flammability, low toxicity and is environmentally friendly. Lilje indicates that the potassium formate-based heat transfer fluid can be used down to a temperature of -45 C. The system can be recharged next to a heat pump without any problem.
The potassium formate-based fluid was evaluated in lab test rigs, as shown in Figure 2. Field trials were initiated in 2003 at two newly constructed houses in northeastern Ohio. Lilje reports that both trials are still going well in 2009.
Figure 2. Lab test rigs were used to evaluate the efficacy of a potassium formate-based heat transfer fluid in a geothermal application used in residential housing. (Courtesy of The Lubrizol Corp.)
The potassium formate heat transfer fluid has been commercialized, and a modified formulation is available for industrial food and pharmaceutical applications.
NATURAL GAS COMPRESSORS
Heat transfer fluids can be used to recover heat from low temperature exhaust for use in power generation in a process called the Organic Rankine Cycle (ORC). Gamble says, “The fluid picks up the heat from an exhaust source, then vaporizes a second working fluid, which passes through a turbine to generate electricity and then recondenses. This process runs in a continuous loop.”
In an application in Canada, Gamble indicated that a synthetic heat transfer fluid has been employed to recover heat from natural gas compressors used on a pipeline to ultimately generate 10-megawatts of electricity from two facilities. The project is driven by a regulation requiring power generators to meet 50% of their new power needs from renewable sources and cogeneration.
Gamble says, “The heat recovery process will ultimately offset between 20,000 and 30,000 tons of greenhouse gases on an annual basis.” A synthetic heat transfer fluid with an operating range up to 290 C was used.
SECONDARY LOOP REFRIGERATION
Demands on refrigeration in supermarkets are quite high with large display cases in the frozen food section needing to be kept cool. Compressors for conventional direct expansion (DX) refrigeration systems are normally housed in a centralized location in the rear of the store (known as a rack). Connor says, “This type of system contains a large number of pipes and fittings which are prone to leak. The result is that an average supermarket system utilizing centralized DX refrigeration can lose as much as 20% to 30% of the primary refrigerant to the atmosphere.”
In a White Paper prepared by Heatcraft Refrigeration Products, a single supermarket may contain up to 5,000 pounds of refrigerant for cooling (
2). The U.S. has approximately 35,000 supermarkets, so the leakage is a considerable environmental and cost problem.
Secondary loop refrigeration has emerged as an alternative approach that reduces refrigerant use and leakage. This method enables a smaller refrigerant system to be used to directly cool the food display cases. The heat transfer fluid utilized in this application is based on propylene glycol. Heat taken away from the food display cases by the secondary loop is transferred to the primary refrigeration system.
An image showing secondary loop refrigeration is provided in Figure 3. One such successful example has been with a Wal-Mart Supercenter near Denver.
Figure 3. Secondary loop refrigeration is being more widely used to cool large display cases in the frozen food section of supermarkets. The propylene glycol-based heat transfer fluid provides better energy efficiency, lower refrigerant costs and reduced maintenance. (Courtesy of The Dow Chemical Co.)
Connor says, “We have found that the propylene glycol-based heat transfer fluid provides good performance in medium temperature secondary loop refrigeration. This technique has significantly improved energy efficiency, lower refrigerant costs and reduced maintenance by as much as 50%.”
The heat obtained from the secondary loop system may also be recovered in an in-store heating loop for such applications as sidewalk snow melting and hot water heating.
Secondary loop refrigeration needs to be conducted in conducive climates. Connor says, “This process will work well in moderate to cool climates but may not necessarily be as effective under hot, humid conditions.”
NANOPARTICLES
Research on the use of nanoparticles in heat transfer fluids has been ongoing for over 15 years. Dr. Jacopo Buongiorno, associate professor of nuclear science and engineering at MIT, says, “The first paper discussing the use of nanoparticles in heat transfer fluids appeared in 1993. The author indicated that nanoparticles enhance the thermal conductivity of the heat transfer fluid.”
Buongiorno noted that some researchers saw enhanced thermal conductivity with nanoparticles while others did not. For example, one researcher reported that the addition of copper nanoparticles with a diameter of about 10 nanometers boost the thermal conductivity of ethylene glycol by 40%. A second researcher published data showing that addition of 1% to 4% by volume of aluminum nanoparticles boosts the thermal conductivity of water by 10% to 25%.
In round-robin testing, among researchers using exactly the same samples in 2008, Buongiorno indicated that the majority of measurements reported improved thermal conductivity with nanoparticles but not to the abnormal extent initially reported in the literature.
Nanoparticles have also been found to boost the heat transfer performance of heat transfer lubricants. Recently, Kedzierski of the NISH indicated that the use of copper oxide nanoparticles in a polyol ester-based refrigeration lubricant increases heat transfer between 50% and 275% (
3).
Nanoparticles also have been reported to boost the critical heat flux (CHF) up to 200% at small concentrations. CHF represents the upper limit of nucleate boiling or formation of gaseous bubbles in a liquid. Any process that can raise the CHF can greatly improve the performance of boiling-based cooling systems.
Buongiorno and Dr. Lin-wen Hu, associate director of the MIT Nuclear Reactor Laboratory, are in the process of evaluating how nanoparticles can improve the performance of heat transfer fluids in nuclear power plants. The type of nuclear reactor being evaluated is the light water reactor (LWR), which uses water as a coolant in regulating the energy generated during the fission process.
The MIT researchers see three potential applications for nanoparticles with LWRs. The first possibility is to utilize nanoparticles in water to boost the power emanating from the reactor core. Nanoparticles suspended in the reactor coolant would boost the CHF, which enables a higher transfer rate for the fission heat.
Buongiorno says, “We have done simulation studies showing a 20% improvement in power density, which is the ratio of the power generated in the reactor core to the volume of the reactor core. But there could be problems with ensuring that the nanoparticles remain physically and chemically stable under the harsh conditions of the reactor (temperature of 300 C and pressure of 150 atmospheres).”
The second application involves using nanoparticles in heat transfer fluids under emergency conditions. In the event of a loss-of-coolant accident in the nuclear reactor, the emergency core cooling system (ECCS) is activated to reflood the core and restore cooling. If nanoparticles are added to the ECCS, the cooling rate can be greatly accelerated.
A third possibility is using nanoparticles in a fluid to cool down the reactor in the event of a severe accident such as a core meltdown. Buongiorno says, “In contrast to the other two applications, the nanoparticle-based heat transfer fluid is injected into the core when needed. This is a straightforward approach in which there is no need to be concerned with nanoparticle stability or compatibility.”
The nanoparticle-based heat transfer fluid would be injected into the space around the bottom of the core. In these hypothetical accidents, the objective is to keep the molten core within the reactor vessel, which is accomplished by flooding the space around the vessel with emergency coolant. If the coolant contains nanoparticles, the core cooling rate can be increased. Buongiorno says, “In contrast to the other two applications, the nanoparticle-based heat transfer fluid is completely separated from the reactor system under normal conditions. This is a straightforward approach in which there is minimal concern about nanoparticle stability or compatibility.”
As it typically takes about 10 years to have any major innovation proposed to the nuclear industry approved by the Nuclear Regulatory Commission, the MIT researchers see the third application as the best possibility for utilization of nanoparticles in nuclear reactors.
The empirical work done by Buongiorno and Hu has been conducted with various oxides (for example, alumina, silica, zinc oxide and zirconia) as well as diamond nanoparticles. An experimental setup is shown in Figure 4. Further information can be found in two recent references (
4, 5).
Figure 4. Experimental setup used to evaluate the effectiveness of nanoparticles in improving the performance of heat transfer fluids in nuclear power plants. (Courtesy of The Massachusetts Institute of Technology)
The MIT researchers are also exploring the use of nanoparticles to enhance the boiling heat transfer properties of refrigerants. Hu says, “Our initial experimental results indicate that a small amount of nanoparticles also can improve the boiling heat transfer performance of refrigerants. This is an important finding for the automobile and power electronics industry that will be under pressure to switch to low Global Warming Potential (GLW) fluids. Adding nanoparticles to new GLW fluids is an option being evaluated to maintain or improve their heat transfer performance and to enable direct drop-in replacement in existing systems.”
Mohapatra has been evaluating the use of diamond nanoparticles in water glycol and oil-based heat transfer fluids. He says, “Diamond exhibits about five to six times better thermal conductivity than metals such as copper. This material is also inert, has good thermal stability and is non-catalytic, which means it will not degrade other components in or coming into contact with the fluid.”
Diamond has a thermal conductivity of about 2,300 Watts/mK. The technology used to prepare the diamond nanoparticles originated in the Soviet Union (
6). Mohapatra says, “We have investigated different nanodiamond particles, including diamond core with a graphene shell, functionalized nanodiamond and nanoparticle clusters.”
The diamond nanoparticles can be dispersed in both oil-and water-based systems (
see Figure 5). Mohapatra remarked that treat rates of 0.1% were used, which only leads to an improvement in the thermal conductivity of 10%. Mohapatra says, “We are working to increase the thermal conductivity of the nanodiamond-based heat transfer fluids by utilizing various dispersion techniques.”
Figure 5. Nanoparticles dispersed in heat transfer fluids have the potential to improve thermal conductivity. (Courtesy of Dynalene Inc.)
Interestingly enough, diamond nanoparticles have been found to boost the fuel economy of trucks. Mohapatra says, “Diamond nanoparticles boosted the fuel economy of diesel trucks by about 4% to 5%. Testing is currently ongoing.”
Mohapatra indicates that a nanoparticle-based coolant has been developed for fuel cells. The function of the nanoparticles in this coolant is to maintain a low electrical conductivity that is essential to the proper functioning and safety of the systems. This fluid is also currently used in computer and electronics cooling applications due to its low electrical conductivity.
FUTURE CHALLENGES
Heat transfer fluid suppliers are looking for future improvements in thermal fluid efficiency. Bates says, “Water is really the most efficient heat transfer fluid but, of course, has a limited temperature range. Our long-term goals are to explore various technologies in the hopes of replicating the efficiency of water across a much wider temperature range.”
One other area of need is that regulatory pressures from insurance companies and fire marshals are mandating that industrial companies operating in their jurisdictions use heat transfer fluids that are below their flash points. This step can improve safety but puts users into a bind. Bates explains, “The problem is that this step can force manufacturers to lower their operating temperatures, find a higher flash point fluid or else cease operations.”
As an example, Bates cites a regulation from the Technical Standards and Safety Authority (TSSA) of Ontario, Canada, that mandates the batch cookers in a rendering operation use fluids at a full 50 F below its flash point. For the specific operation, this means a fluid is required with a flash point above 260 C.
Fortunately, Bates says, “We have been proactive in developing high flash point fluids to meet these stringent requirements and were able to keep this customer cooking.” In the future, this customer will be setting up a gasification system to destroy contaminated beef protein. The system will use a heat transfer fluid to capture the heat generated and use it in the rendering operation.
As energy efficiency becomes more important, heat transfer fluids will play a larger role in providing effective solutions. Particularly important will be applications that can utilize heat in a more productive manner.
REFERENCES
1.
Greiner, H. and Bussick, F. (2000), “Mechanical Sealing for Heat Transfer Fluids,”
Lubrication Engineering,
56 (8), pp. 17–24.
2.
DelVentura, R., Evans, C. and Richter, I. (2007), “Secondary Loop Systems for the Supermarket Industry,”click
here.
3.
Canter, N. (2008), “Improving Refrigeration with Nanoparticles,” TLT,
64 (11), pp. 14–15.
4.
Kim. S., Bang. I., Buongiorno, J. and Hu, L. (2006), “Effects of Nanoparticle Deposition on Surface Wettability Influencing Boiling Heat Transfer in Nanofluids,”
Applied Physics Letters,
89 (15), p. 153107.
5.
Buongiorno, J., Hu, L., Kim, S., Hannink, R., Truong, B. and Forrest, E. (2007), “Nanofluids for Enhanced Economics and Safety of Nuclear Reactors: An Evaluation of the Potential Features, Issues and Research Gaps,”
Nuclear Technology,
162 (1), pp. 80–91.
6.
Vereschagin, A., Petrov, E., Sakovich, G., Komarov, V., Klimov, A. and Kozyrev, N. (1999), “Synthetic Diamond-Containing Material and Method of Obtaining It,” U.S. Patent
5,861, 349.
Neil Canter heads his own consulting company, Chemical Solutions, in Willow Grove, Pa. You can reach him at neilcanter@comcast.net.