BAM: Antiwear and friction-reducing coating
Dr. Neil Canter, Contributing Editor | TLT Tech Beat March 2009
A two-phase submicron microstructure is produced when mixing BAM with titanium diboride.
KEY CONCEPTS
•
An alloy of boron-aluminum-magnesium (AlMgB14, nicknamed BAM), with the addition of titanium diboride displays exceptionally strong hardness.
•
The coefficient of friction for the BAM-titanium diboride alloy ranges between 0.02 and 0.10.
•
The BAM, titanium diboride alloy is being evaluated as a coating on a rotary vane pump and as a tool coating in machining.
Reducing wear and friction remains a constant goal to improve the efficiency, decrease energy costs and extend the life of machinery. Both liquid and solid lubricants play an important role in providing antiwear and lubricity characteristics to achieve these results.
One solid coating that has gained more attention recently is an alloy of boron-aluminum-magnesium (AlMgB14, nicknamed BAM) prepared initially with addition of silicon and more recently titanium diboride. BAM was found to exhibit exceptionally strong hardness in 1999 by researchers at the U.S. Department of Energy’s Ames Laboratory.
Alan Russell, Ames lab scientist and professor of Material Science and Engineering at Iowa State University, in Ames, Iowa, says, “BAM by itself displays a hardness between 30 and 32 gigapascals. Titanium diboride also has a similar value, but when we combine the two materials a synergy develops that leads to an improvement in hardness.”
Russell adds, “Mixing BAM with titanium diboride produces a two-phase submicron microstructure that leads to an increase in hardness that ranges between the mid-30s and low-40s gigapascals, depending on the ratio of the two components.”
Project leader Bruce Cook and Russell believe that BAM and titanium diboride generate a strong bonded interface between the two materials. This interface inhibits crack formation.
The coefficient of friction for the BAM-titanium diboride alloy ranges between 0.02 and 0.10, according to Russell. He adds, “The high boron content contributes to the low coefficient of friction. In contrast, polytetrafluoroethylene exhibits a coefficient of friction between 0.05 and 0.06.”
With its interesting properties, the BAM alloy has the potential to be useful in lubricant applications. Russell says, “We consider it to be not really a lubricant but to act as a lubricant.”
LUBRICANT APPLICATIONS
The BAM alloy is currently under evaluation by industry partners as a coating on a hydraulic pump and on cutting tools for metalworking applications. Several techniques have been used to introduce the BAM alloy onto substrate surfaces.
Russell says, “We use pulsed laser deposition that enables the user to apply the exact stoichiometry desired. The one limitation is that of sample size.”
Russell indicated that industry partners evaluating the BAM alloy use more efficient techniques such as magnetron sputtering to apply the coating. He adds, “No incompatibility problems have been seen with the substrates used to date. Those include various steel alloys (such as tool steel and low carbon steel), tungsten carbide and pure silicon.”
Feedback from these partners indicates that the BAM alloy coatings are extremely durable. For example in cutting tools, the BAM alloy displays particularly high wear resistance vs. such alternative coatings as cubic boron nitride and diamond. The coatings used are typically two to three microns in thickness.
Rotary vane pumps can generate friction when the vanes contact the housing or stator. Currently, a hard tool steel which is prepared by quenching is used, but this alloy is tough to machine and expensive.
Russell says, “An industry partner applied the BAM alloy coating to an ordinary alloy steel and found that the horsepower required from the pump dropped at startup by 6% to 8%. During steady state operation, the horsepower requirement of the pump declined by 3%.”
The savings in energy may allow the industry partner, an OEM supplier of pumps, to downsize the motors. Russell says, “A switch to a more environmentally acceptable fluid also is being evaluated as a means to improve cost performance and safety.” The industry partner may begin commercializing pumps containing the BAM alloy coating in 2010.
One particularly promising application area in tool coatings is titanium machining. This metal is widely used in aerospace applications. Russell says, “Titanium is a highly reactive metal under high temperature machining conditions of 400 C or higher. This metal tends to dissolve tools.”
The BAM alloy is relatively inert toward titanium as evaluated in a very rigorous test. Russell explains, “We placed pieces of titanium and steel in a press and forced them together at a pressure of 10 megapascals and a temperature of 1,000 C for a few hours. At the end of the procedure, the steel and titanium were welded together and could not be separated. When the test was run with a BAM-coated steel piece and titanium, the two pieces fall apart when removed from the die.”
In testing conducted by an industry partner, tools coated with the BAM alloy displayed 20% to 40% better life during machining of a titanium alloy. Russell says, “This result is leading our partner to look at machining titanium at higher cutting speeds to improve productivity.” The BAM alloy coating is also useful in machining other alloys such as the stainless steel shown in Figure 1.
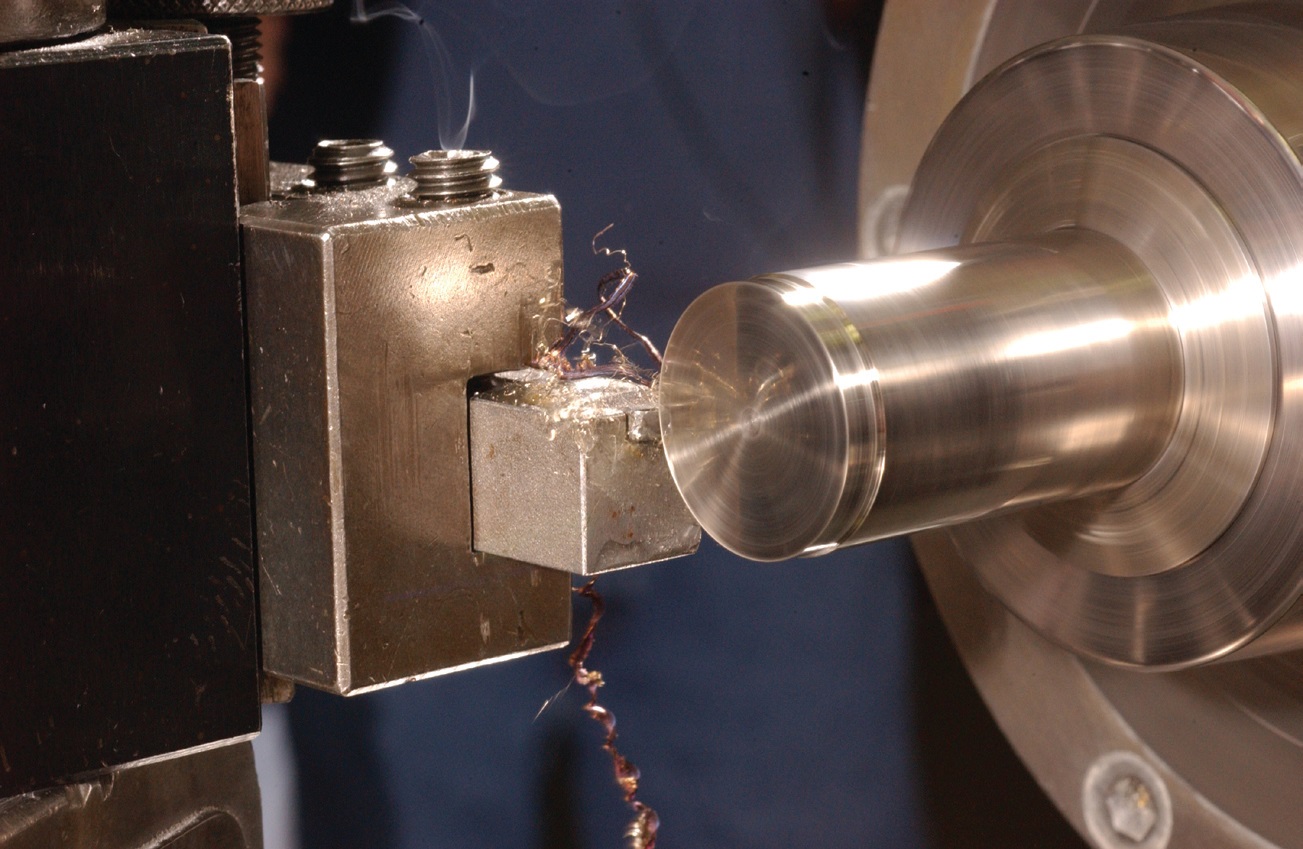
Figure 1. The BAM-titanium diboride alloy exhibits exceptional hardness that can be used as a tool coating to machine alloys such as stainless steel. (Courtesy of the U.S. Department of Energy’s Ames Laboratory.)
Other applications that Russell envisions for the BAM alloy include as a coating on camshafts and bearings of heat engines. He adds, “Bulk BAM alloy also could be used in abrasive cutting tool nozzles in place of titanium carbide or sapphire. For this demanding application, even a BAM alloy coating would wear away.”
Additional information on the BAM alloy can be found in a U.S. Patent (
1). The BAM technology has been licensed for commercialization applications to Newtech Ceramics of Des Moines, Iowa. Further information can be found at
www.newtechceramics.net.
REFERENCE
1.
Cook, B., Harringa, J. and Russell, A. (2000), “Superabrasive Boride and A Method of Preparing the Same by Mechanical Alloying and Hot Pressing,” U.S. Patent 6,099,605.
Neil Canter heads his own consulting company, Chemical Solutions, in Willow Grove, Pa. Ideas for Tech Beat items can be sent to him at neilcanter@comcast.net.