The Possibilities and Limitations of Dry Machining
Dr. Neil Canter, Contributing Editor | TLT Metalworking March 2009
Dry and near-dry machining won’t replace traditional metalworking fluid technology anytime soon, but they do offer advantages for some niche markets.
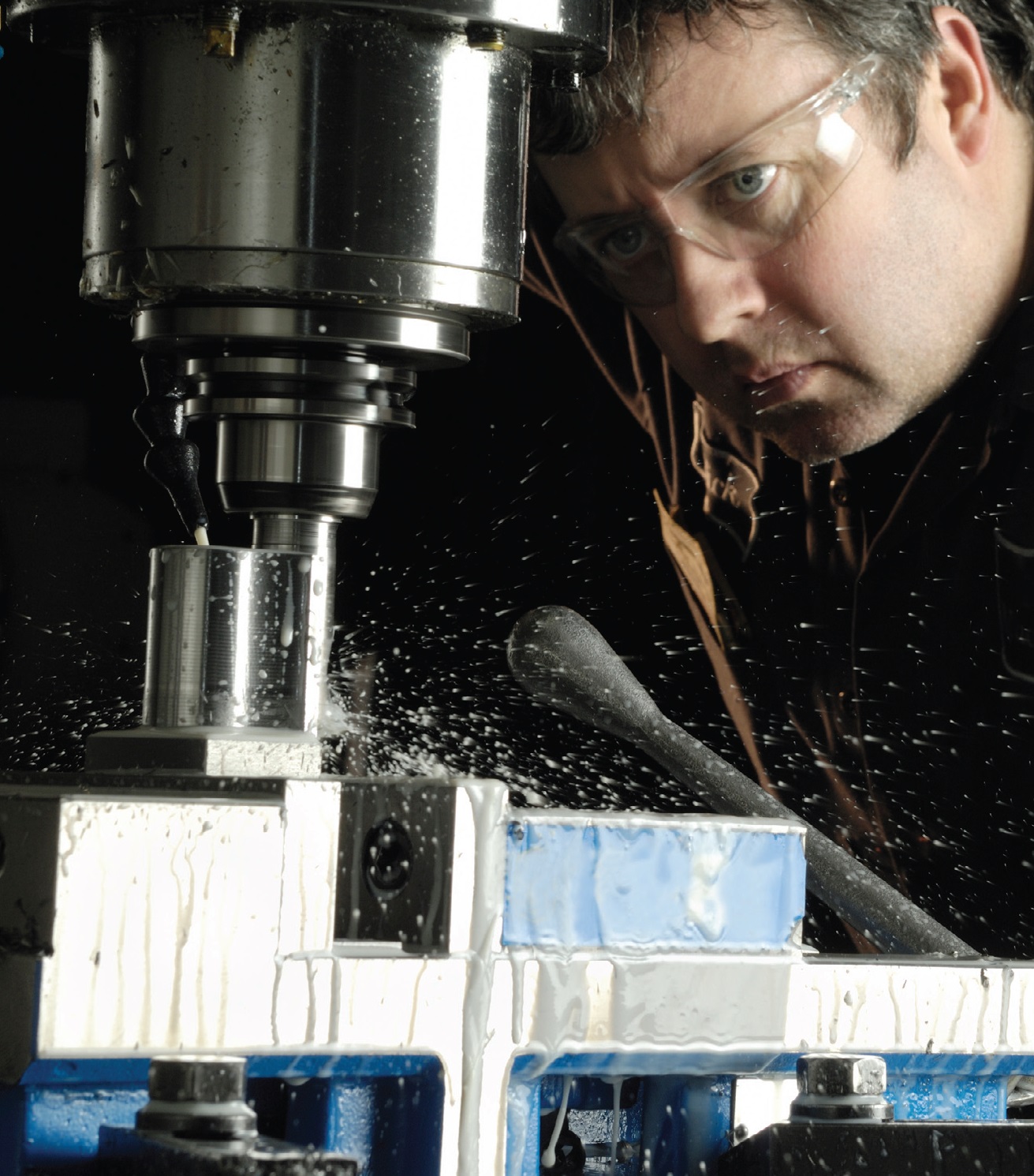
Metalworking fluids have undergone intense regulatory scrutiny during the last 20 years.
KEY CONCEPTS
•
Dry machining and near-dry machining are two processes MWF end-users are using to reduce costs and improve productivity.
•
Several machining operations are comprised of metalworking and have different requirements on the lubricant.
•
One of the perceived difficulties of near-dry machining is chip removal.
Metalworking fluids are known to provide many benefits to ensure that metal parts can be machined in a cost-effective manner. The positive features of metalworking fluids have long been established and include friction reduction, cooling, corrosion protection, welding protection from the tool to the workpiece and the washing away of metal chips.
But metalworking fluids have undergone intense regulatory scrutiny during the last 20 years. The United Auto Workers petitioned the Occupational Safety and Health Administration (OSHA) to lower the permissible exposure limit for metalworking fluids from 5.0 mg/m3 to 0.5 mg/m3. In response, OSHA established the Metalworking Fluid Standards Advisory Committee (MWFSAC) in 1997 to develop standards or guidelines related to metalworking fluids. In its final report in 1999, MWFSAC recommended that the exposure limit be 0.5 mg/m3 and that medical surveillance, exposure monitoring, system management, workplace monitoring and employee training are necessary to monitor worker exposure to metalworking fluids.
In the current, competitive manufacturing environment, end-users of metalworking fluids are looking to reduce costs and improve productivity. The costs of maintaining and eventually disposing of metalworking fluids, combined with the aforementioned health and safety concerns, have led to a heightened interest in either eliminating metalworking fluid altogether or limiting the amount of metalworking fluid applied. The former process is known as dry machining while the latter is referred to as near-dry machining or minimum quantity lubrication.
Different segments of the metalworking community have estimated metalworking fluid costs in several fashions. Data from tool coatings manufacturer Balzers Inc., headquartered in Amherst, N.Y., estimates the cost of metalworking fluids to be 16% of the total cost incurred by a typical end-user, as shown in Figure 1. In contrast, STLE-member Doug Hunsicker, a retired senior engineering specialist for Caterpillar in Peoria, Ill., estimates that metalworking fluids represented 0.9% of his company’s total manufacturing costs in 2001.
Figure 1. Typical End-User Manufacturing Costs
Due to the importance of using metalworking fluids, elimination of these lubricants has become quite challenging. A tremendous amount of heat and friction is generated as a cutting tool drives into a workpiece. STLE-member Dr. Emmanuel Ezugwu with The School of Engineering Systems & Design at London’s South Bank University, reports that 70% of the heat generated in machining originates with plastic deformation of the workpiece. The remaining 30% of the heat arises from friction at the chip/tool and tool/workpiece interfaces (
1). Without metalworking fluid, excessive tool wear and inferior surface finish may occur during machining. Both of these factors significantly increase manufacturing costs and reduce productivity.
THE DRY-MACHINING CHALLENGE
Metalworking is composed of a number of different machining operations that place different requirements on the lubricant. Other parameters that must be considered are the alloy of metal being machined, the machine tool and the cutting tool used in the process.
“Some machining operations are more amenable to dry machining than others,” says John Sutherland of Michigan Technological University in Houghton, Mich. “open-faced operations such as milling and boring can be effectively run dry.” The resulting chips can be easily moved away from the tool/workpiece interface. In these cases, there is not as great a need for lubricity, and the heat generated can be managed.
In contrast, closed-face machining operations such as drilling and tapping cannot be efficiently run dry because the metal chip remains in close proximity to the tool/workpiece interface. This possibility increases the prospects of chips damaging the tool and the workpiece surface because there is no mechanism in place for their removal.
Sutherland reported on early dry-machine studies involving the drilling and boring of cast aluminum alloys in 1998 (
2). In those studies, dry machining proved lacking because feed rates needed to be decreased in order to avoid compromising surface finish requirements.
CUTTING TOOL COATINGS
Advances in the types of coatings applied to cutting tools have been the major factor in improving the feasibility of dry machining. Just four years ago, the leading tool coating was aluminum oxide. But coatings based on titanium nitride (TiN), titanium carbon-nitride (TiCN) and titanium aluminum nitride (TiAlN) have been developed to withstand more severe operating conditions.
In particular, TiAlN has emerged because this coating exhibits thermal stability up to a temperature of 900 C. Coatings increase tooling costs by an average of only 10%. Torsten Doering, Balzers market manager, indicated that his company has combined TiAlN with tungsten carbide carbon to generate even better tooling performance. “This coating displays a very low friction coefficient, enabling its use in deep hole drilling under almost dry conditions,” he says.
Dennis Quinto, technical director for Balzers, indicated that mold steels such as 4140 and 4340 can be milled and shaped with coated tooling. These alloys typically have Rockwell hardness ratings (HRC) ranging from 52 to 58 HRC. But there are limitations because metals such as titanium and stainless steel are not amenable to dry machining. The former metal exhibits a very low thermal conductivity rating, which means that heat cannot be effectively carried away from the tool/workpiece interface. Stainless steel machining typically produces long chips that extend the contact length between the chip and the tool and, as a consequence, increases the amount of heat in the cutting zone.
Milling is a popular operation to run dry, particularly because tool life can be superior under dry as opposed to wet conditions, according to Quinto. “Coolant use in milling leads to higher fluctuations in the temperature of the cutting edge as the tool goes in and out of the cut,” he says. “This effect can cause thermal cracking, leading to premature tool failure by edge microfracture. Under dry conditions, the temperature does not change that dramatically, which extends the life of the tool.”
Ezugwu indicated that coated cutting tools can be used without metalworking fluid in hard turning. This finishing process is used on steels with hardness ratings above 60 HRC at cutting speeds two to four times higher than those used for conventional cutting tools.
DRY MACHINING LIMITATIONS
While the technology to carry out dry machining has improved, metalworking fluid is needed to ensure that higher speeds and feeds can be used and to ensure that the surface finish of workpieces meets expectations. Hunsicker revealed that Caterpillar has tried dry machining in a number of machining operations during the past 20 years. The new tool coatings have been helpful but still the problem exists that machining cannot be done dry at the rate needed to achieve the productivity found with using metalworking fluids.
STLE-member John Cutcher, technical director for D.A. Stuart Co. in Warrenville, Ill., has not seen any increase in dry machining beyond its use on cast iron. He believes that dry machining cannot overcome the positive benefits of using metalworking fluids. One other factor to consider is the production of particulate. Cutcher claims that dry machining can produce as much air particulate as wet machining. Data supporting Cutcher has been published by Woskie et.al (
3).
Timothy Ovaert of the University of Notre Dame in South Bend, Ind., believes the lubricious coatings on cutting tools do not last long enough to deliver the productivity needed in today’s manufacturing environment. Most of the research in this area originated in Europe where end-users deal with more expensive disposal costs than in North America. In using metalworking fluids, end-users face a tradeoff between disposal costs and productivity.
Says Ovaert: “There is a need for developing better technology to dry machine, specifically in the area of managing the formation and removal of the chip. State-of-the-art tool coatings must be designed that are both economical (in terms of large batch deposition processes) and engineered at the atomic scale to ensure that the coatings stay put over a long operating time frame and perform multifunctional tasks.”
NEAR-DRY MACHINING
Near-dry machining involves the application of small amounts of lubricant to the tool/workpiece interface. The key to the process is atomizing the lubricant, with air as the carrier, into a fine aerosol. In contrast to dry machining, the lubricant is available to facilitate machining operations such as drilling.
Lee Hitchcock, research chemist for ITW in Glenview, Ill., indicated that near-dry machining can be carried out on many machining operations. Applications such as sawing are well suited for near dry machining. The lubricants used are vegetable oil-based products priced between $20 and $60 a gallon.
While the price is higher than most coolants used in conventional applications, the use rate is two ounces per eight-hour shift, according to Rob Myers, business unit manager for ITW. Myers pointed out that coolant applied by the flooded method cannot be used in near-dry machining. He indicated that the latest development in near-dry machining is the application of the lubricant directly through a hole in the cutting tool. This is analogous in wet machining to delivering the metalworking fluid through the spindle.
Horkos Corp. of Japan has been a pioneer in the development of machine tools for use in near-dry machining (
see examples in Figures 2 and 3). The company has developed a delivery system in which air and oil are mixed as closely as possible to the cutting tool, as shown in Figure 4.
Figure 2. A cylinder head being processed with HORKOS’ near-dry technology (Courtesy of Horkos Corp.)
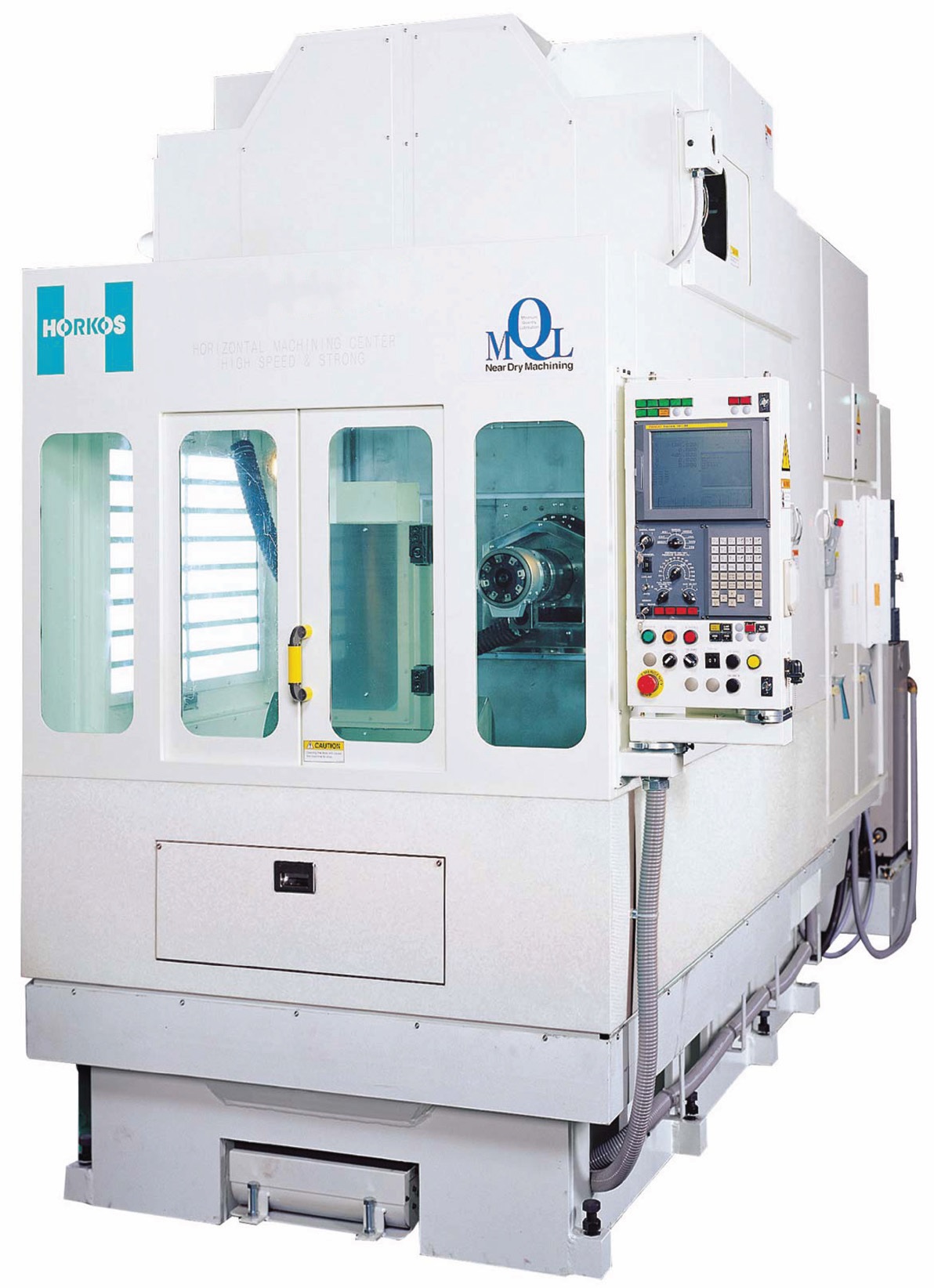
Figure 3. Full-view model of HORKOS’ RM70H Machining Center (Courtesy of Horkos Corp.)
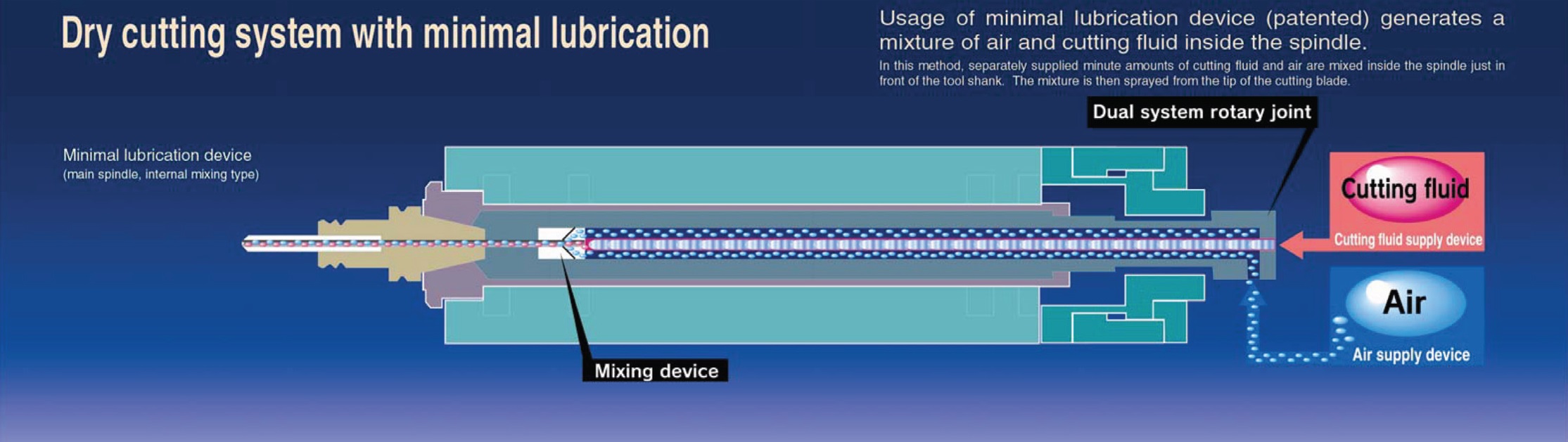
Figure 4. Cross-section of a spindle and the two-channel minimum quantity lubrication delivery system (Courtesy of Horkos Corp.)
Mark Ostraff, sales manager for Marubeni America in Canton, Mich., (the U.S. representative for Horkos) indicated that near-dry machining has been more popular in Japan and Europe than in the United States. Horkos found that near-dry machining is most effective on cast aluminum alloys and steel alloys in operations such as gun drilling and deep hole drilling.
One of the perceived difficulties of near-dry machining is chip removal. Horkos eliminated this problem by using a combination of a gravity drop and vacuum method. Ostraff co-authored a study using the Horkos technology to near-dry machine aluminum (
4).
Near-dry machining does have its limitations, especially with regard to high-volume machining. Hitchcock indicated that if multiple operations are done in a short period of time not enough nozzles can be employed to direct sufficient metalworking fluid to the tool/workpiece interface of each operation. Cutcher said that the cost of near-dry machining is higher than conventional machining because the lubricant is used neat and is utilized in one pass instead of recirculated. A recent study on near-dry machining indicated that the mist generated by this technique was higher than seen with wet machining (
5).
DRY MACHINING’S FUTURE
While dry and near-dry machining will not, in the near future, replace wet machining, these two techniques will provide cost-effective alternatives in niche applications.
One large OEM has been developing techniques to effectively dry machine and is close to moving this technology from R&D onto the shop floor.
The function of the metalworking fluid when used with coated tooling may also change, as was described by Hunsicker. Traditional thinking dictates that a heavy-duty soluble oil formulated with extreme pressure additives be used in a high-speed turning application. However, when the operation was conducted, Hunsicker found that the soluble oil stripped the coating from the cutting tool. Caterpillar determined that use of a synthetic metalworking fluid produced superior performance. The main role of the metalworking fluid in this case was to efficiently remove the heat generated. Ovaert also has indicated that metalworking fluid additive suppliers and formulators could be very helpful in providing technology to improve the durability of tool coatings.
REFERENCES
1.
Ezugwu, E.O. and Olajire, K.A., (2001), “Assessment of Dry Cutting and Low Dose Coolant Supply in Machining,” STLE Preprint 01-NP-4, Presented at the STLE 56th Annual Meeting in Orlando, Fla.
2.
Batzer, S., and Sutherland, J., (1998), “The Dry Cure for Coolant Ills,”
Cutting Tool Engineering,
51 (4), pp. 34-44.
3.
Woskie, S.R., Smith, T.J., Hammond, S.K. and Hallock, M.H. (1994), “Factors Affecting Worker Exposure to Metalworking Fluids During Automotive Component Manufacturing,”
Appl. Occup. Environ. Hyg.
9 (9), pp. 612-621.
4.
McCabe, J. and Ostraff, M.A., (2001), “Performing Experience with Near–Dry Machining of Aluminum,”
Lubrication Engineering,
57 (12), pp. 22-27.
5.
McClure, T.F. and Gugger, M.D., (2002), “Microlubrication in Metal Machining Operations,”
Lubrication Engineering,
58 (12), pp. 15-21.
Neil Canter heads his own consulting company, Chemical Solutions, in Willow Grove, Pa. You can reach him at neilcanter@comcast.net.