I get misty … no more!
Dr. Robert M. Gresham, Contributing Editor | TLT Lubrication Fundamentals March 2009
Controlling mist contamination is a top priority for metalworking fluid managers in protecting the environment of their operations.

KEY CONCEPTS
• Mist can be measured in a variety of ways with equally varying amounts of expense and accuracy.
• Mists are considered an acceptable risk to employees in MWF plants, according to several published standards.
• Not all respiratory problems come from particulate mists. Others include chemicals and biological agents such as bacteria, mold and bacterial decay products.
Many of TLT’s younger readers probably have never heard of the song “Misty,” most popularly sung by the great Johnny Mathis. For a brief time “Misty” was even the theme for “The Today Show,” when a very young Barbara Walters was its first-ever female host. In 1971 jazz enthusiast Clint Eastwood directed the thriller, “Play Misty for Me,” where he played a disc jockey stalked by a deranged female fan.
Written and recorded in 1959 as a soft ballad, “Misty” came before folk, acid rock, heavy metal and rap music—it had musicality and harmony, and the average person could hum, whistle or sing it. I was a child at the time “Misty” was released. While doing a little free association for this article, the song came to mind when thinking about today’s metalworking plants.
In the old days it was pretty easy to “get misty” in metalworking operations due to the mist generated when workplace, tool and metalworking fluid interacted. In fact, in many of these plants you could hardly see from one end of the building to the other due to this kind of mist, not to mention the odor and effect on one’s lungs.
At least in most developed countries, those days are also pretty much in the past or at least receding rapidly. But it wasn’t easy to stop “getting misty.” And it takes constant vigilance by metalworking fluid managers to avoid getting misty again. Let’s take a look at what these managers must deal with.
MIST CHEMISTRY
Mist can be a combination of smoke, spray and/or aerosol resulting from elevated temperatures, both atmospherically or in a specific machining process, mechanical action and/or bubbling of the machining fluid. Smoke can result as fluid enters the hot cutting zone, and volatile components of the fluid vaporize. These vapors in turn re-condense to form small particles (~1 μm) seen as smoke. Thus, the chemical composition of the smoke reflects mostly the volatile ingredients. These small particles or droplets are small enough to float over large areas of the shop.
Spray arises from mechanical motion and causes mist as the fluid hits a rotating tool or part or stationary parts of the machine and is broken into large droplets (10 μm). Thus, the droplets have the same composition as the bulk fluid. These droplets settle rapidly from the air, causing local exposure only.
Aerosols result when moving fluid comes to rest, allowing entrained air to escape; mist rises from the surface as the bubbles break. Some components can be selectively concentrated in this aerosol, primarily short chain organic acids. These components are often associated with respiratory irritation. These droplets are small (~1 μm) and can float throughout the shop area.
However, mists are not the only thing contaminating the atmosphere of a metalworking plant. In addition, we often have metal dust, tow motor exhaust, welding fumes, degreasing fumes, washer mist and common dirt with which to contend. Thus, it is important that the fluid manager make certain that he is addressing the correct problem in controlling the atmosphere of the plant.
TACKLING MIST
Mists can be measured in a variety of ways. While it goes beyond the scope of this article to get into greater detail, it can be said that mists can be measured with equally varying amounts of expense and accuracy: Gravimetric (total), Extraction (total), Combined (total), Infrared (total), Impactors (gravimetric), Electrostatic precipitation (gravimetric) and Light scattering (qualitative).
Gravimetric methods usually involve personal sampling where air is drawn across a filter worn by an operator for a designated time period. The filter then is analyzed by various methods. Light scattering, while qualitative, can provide useful information regarding specific locations or machines in the plant where mists are being generated or where ventilation is inadequate.
There are a number of published standards where mists are considered an acceptable risk to the employee. These are: OSHA PEL (permissible exposure limits): 5 mg/m3, mineral oil mist (Note: ACGIH has published a Notice of Intended Change, to 0.2 mg/m3, mineral oil, A2 or A4 designation); and NIOSH REL (recommended exposure limit), 0.5 mg/m3, total particulate mass. Of these, the NIOSH REL appears to be the industry’s overall accepted limit for exposure.
It is difficult for the layperson to put these standards into perspective except to say that modern metalworking plants are clean, safe and attractive places to work. They no longer look like opium dens in the 1940s. Most modern large plants with relatively new machines (the older models tend to produce more mists), typically attain the desired RELs. The trend in all plants is clearly in this direction.
Aside from aesthetics, mists can cause respiratory problems. Note that not all respiratory problems come from particulate mists. There also are chemicals (both particulates and vapors) and biological agents such as bacteria, mold and bacterial decay products (endotoxins).
What we can say about particulate mists is that they arise from physical processes. Irritation complaints are common when mist levels exceed 2 mg/m3 for any fluid. Irritation also has been reported at levels well below 0.5 mg/m3 when there were high microbial counts. Metal-removal fluids are alkaline (pH 9) and thus have inherent irritation associated with their use. Some chemicals associated with irritation have been found to be concentrated in mists. Some mists arise from non-metalworking fluid sources.
Chemical managers control mists by proper ventilation; controlling fluid flow rate and method of application; use of enclosures, guards and shields; controlling the specific operation, both machines and process; using mist collectors; strategic placement of machines with respect to flumes; the number of machines in a given area; fan placement; tramp oil levels; microbial levels and overall housekeeping. A good resource for how to control mists is ASTM E1972, Practice for Minimizing Effects of Aerosols in the Wet Metal Removal Environment.
In addition, STLE-members Drs. John Howell with Primagy Consultants Inc., Eugene White with Milacron Inc. and consultant Bill Lucke are the leading industry experts in this area. John and Eugene also teach students about mists and other health and safety topics in STLE’s Total Metalworking Fluids certificate course. As a result of their work, and that of many others, the metalworking industry has made enormous progress in controlling the environment of their operations.
So next time you think, “I get misty…,” the “chances are” you really shouldn’t!
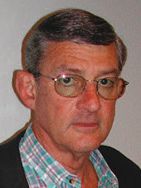
Bob Gresham is STLE’s director of professional development. You can reach him at rgresham@stle.org.