20 Minutes With Dr. Maura Sheehan
Thomas T. Astrene, Publisher | TLT 20 Minutes March 2009
She chaired the OSHA committee responsible for a landmark study on MWFs and offers a 13-point plan for improving industrial health and safety.
PROFILE
Education
• Doctor of Science in Industrial Hygiene (1981), University of Pittsburgh, Pittsburgh, Pa.
• Master of Science in Environmental Studies (1976), University of Lowell, Lowell, Mass.
• Bachelor of Science in Biology (1972), Lowell Technological Institute, Lowell, Mass.
Certification
• Certified Industrial Hygienist (CIH) since 1984.
Editor’s Note: Dr. Sheehan’s name was submitted for a 20 Minutes profile by STLE’s Safety, Health & Regulatory Affairs Technical Committee.
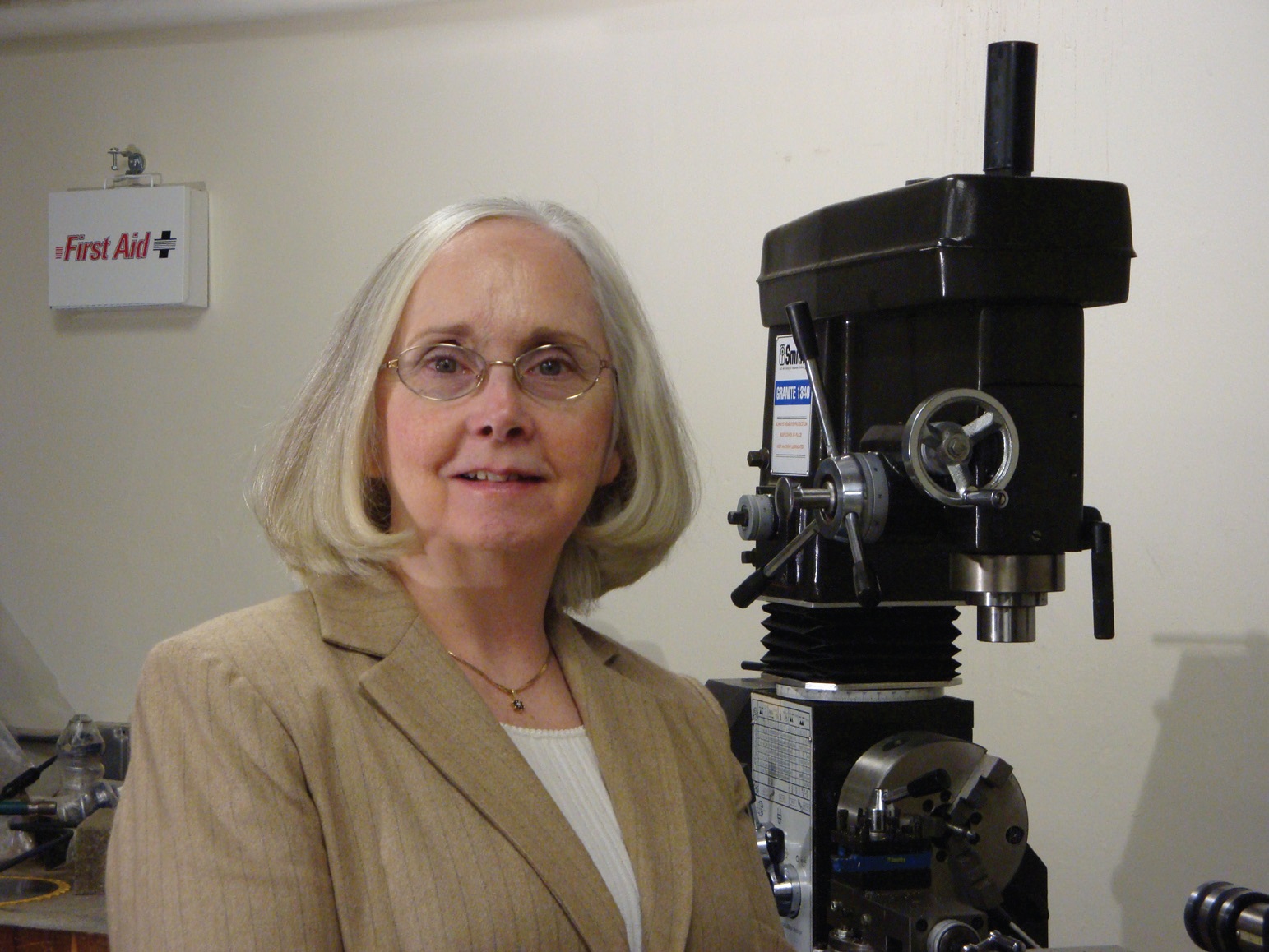
Dr. Maura Sheehan
TLT: Tell us about your unique background.
Sheehan: While working on my master’s degree, I taught lab techniques to wastewater treatment plant operators. Since 1980 I have taught and conducted research at West Chester University in West Chester, Pa., where I am a professor of Environmental Health. I teach a variety of courses at the graduate and undergraduate level, including Industrial Hygiene, Environmental Toxicology, Bioterrorism and Public Health and general Environmental Health courses.
My research area is aerosol science, and I have studied metalworking fluid mist, composite dust, bioaerosols and, most recently, nanoparticles. My focus has been on the control of these aerosols in the workplace and the generation of aerosols for instrument development and toxicology research.
In 1997 I was selected by OSHA to chair the agency’s Metalworking Fluids Standards Advisory Committee (MWFSAC). In 1999 we completed our work and, with the committee’s input, I wrote and submitted the 350-page report of our committee’s deliberations and recommendations. The main body of the report is available on the OSHA Web site.
I have various publications in the aerosol field and am especially proud of the publication Metalworking Fluid Mist—Personal Exposures and Area Concentrations: A Comparison of New and Old Transmission Case Lines,
Journal of Occupational and Environmental Hygiene 4: 288-300, Sheehan, M. and Hands, D. (2007). Dave Hands (Ford Motor Co.) and I were given the American Industrial Hygiene Association’s David Swift Best Aerosol Paper Award of 2007 for this effort.
The data collected for this publication helped prove the technological feasibility for reducing exposure to MWFs to less than 0.5 mg/m
3. In addition to my teaching and research, I am very active in the American Industrial Hygiene Association (AIHA) as a member and past officer of the association’s Aerosol Technology Committee, and I am currently serving as a director of the AIHA Philadelphia Section. I serve my community as chairperson of my township’s Environmental Advisory Committee.
TLT: What was the path that led to you chairing OSHA’s MWF Standards Advisory Committee?
Sheehan: In 1995 I was the chairperson of AIHA’s Aerosol Technology Committee and was encouraged by colleagues to attend the first MWF Symposium because MWF mist was a critical emerging issue for my committee. At the symposium I caught the bug and became fascinated with MWF mist.
With my expertise in aerosols and as a result of that conference I was asked to collaborate on a retrospective study about mist controls with Dave Hands, Dr. Hank Lick and Ben Wong from Ford Motor Co. Our study, Comparison of Metalworking Fluid Mist Exposures from Machining with Different Levels of Machine Enclosure, was published in 1996 in the
AIHA Journal. Our collaboration improved understanding about control techniques, and although I did not have any formal arrangement with or financial remuneration from Ford, Dave’s and Hank’s mentoring about MWFs was invaluable. I was given an intensive “course” on MWFs by attending Ford’s engineering meetings and visiting most of Ford’s machining plants.
On my own I furthered my understanding of MWFs through literature research and the Society of Manufacturing Engineers’ excellent short courses, Coolant Management, and Metalworking Fluids. In May 1996 I organized and chaired two roundtables about MWFs at the AIHA national conference in Washington, D.C. Roundtable participants included representatives from labor, management and academe, and we helped educate the industrial hygiene community about MWFs.
In 1996 I was nominated for OSHA’s MWF Standards Advisory Committee (MWFSAC), and in August 1997 I was asked to chair the committee. The MWFSAC charter ran from August 1997 to August 1999, and I submitted our final report ahead of schedule on July 15, 1999.
Figure 1. Dr. Maura Sheehan, a certified industrial hygienist for 25 years, has been teaching environmental health courses at West Chester University since 1980. Here she is using a microscope to analyze dust samples and microorganisms.
TLT: What kinds of research activities relating to industrial fluids have you been involved in academically? What needs to be done to foster the activities of university researchers?
Sheehan: My research on MWFs focuses on evaluating control strategies. Several presentation opportunities resulted from the work with Ford, including local and national conferences and an international presentation at the International Aerosol Conference in Edinburgh, Scotland. I assisted the National Institute for Occupational Safety and Health (NIOSH) colleagues with the development of a checklist for evaluating MWF worksites, and this led to presentations by these colleagues. I developed research projects with two of my students. One of these students presented this material at a national meeting. I am planning to evaluate mist-generation properties of MWF.
For most researchers, funding is the major factor determining interest and focus for their research. Many researchers are not fully subsidized by university funds and have to cover their salaries and those of research assistants and graduate students. In my case, the work I did with Ford colleagues was done
gratis during the summer or during a sabbatical so I could learn as much as possible about MWFs. It was a true collaboration and educational opportunity but a luxury few researchers (including myself now!) can afford.
Over the years, the most successful programs to develop research data were due to the UAW-Big Three Auto joint research funds. In universities and at auto plants, theoretical and empirical research furthered our understanding of MWFs. For example, techniques to understand droplet generation were developed and better mist collectors were designed.
These collaborations included university researchers and auto company industrial hygienists. The UAW-Big 3 Auto joint funds model could be expanded and include unions, end-users and fluid manufacturers in a broader collaboration with universities. Besides funding, academic freedom is a core value for professors, so companies need to provide guarantees about the freedom to publish findings without restriction.
TLT: What roll do you think university researchers can play to foster H&S in machining environments? Do industrial facilities tend to cooperate with investigators?
Sheehan: University researchers can provide technical expertise to solve specific problems such as designing a mist control device or evaluating H&S programs. Students under faculty supervision can collect exposure assessment data to aid company industrial hygienists.
Some plant managers are very wary of anyone including corporate H&S staff, university researchers and, of course, regulators! The plant manager really sets the tone of either obstruction or collegiality. If there is a recognized and accepted problem to solve, the experience is usually more welcoming.
TLT: Please discuss the key issues raised by the MWFSAC Report.
Sheehan: The key issues raised by our deliberations and our report included specific health effects, how we can better protect workers from these effects and how to accomplish this goal in a manner that is economically and technologically feasible. The accepted health effects of concern included: asthma, hypersensitivity pneumonitis, other respiratory disorders and dermatitis. There was significant debate about cancer, a debate which continues today. Of course, the issue of the relative risks of “used” vs. “new” fluids was discussed.
There was unanimous support for the use of systems management to control exposure to metalworking fluids used in cutting, machining, grinding and honing, essentially metal-removal fluids. Limiting our recommendations to these fluids should not imply a lack of potential problems with other MWFs, only that we had and still have the most data about metal-removal fluids. As we stated in the report, “Systems management includes a comprehensive programmatic approach with enclosure, ventilation, fluid management and other actions to control exposure and minimize contact with the fluid.” Today I would also include comprehensive, responsible and accountable
product stewardship as part of systems management.
While a minority of the committee supported non-regulatory alternatives, the majority supported a defined occupational exposure limit and comprehensive standard including medical surveillance, exposure monitoring and training. Existing (in 1999 and today) OSHA and consensus standards are not adequate or appropriate for MWFs.
The committee recommended a permissible exposure limit (PEL) of 0.4 mg/m
3 thoracic (0.5 mg/m
3 total). At that time, and today there is evidence of adverse health effects below the committee recommended PEL; medical surveillance allows early detection of adverse health effects and leads to better health outcomes.
We viewed training of employees about MWFs as essential and part of OSHA’s role. We believe that our recommendations were technologically and economically feasible, but the committee recognized that a phase-in period was reasonable to reduce cost.
TLT: What do you think the report’s influence(s) has been on promoting H&S in the metalworking fluids industry? Do you think that the OSHA MWFSAC should be reactivated?
Sheehan: Our committee’s existence accelerated work done by NIOSH and research done by industry, labor and academe. We provided input to the ORC Web site and ILMA’s stewardship program. Our report provided the evidence and much of the content for OSHA’s Best Practices for MWF document.
Many of our committee members and participants at our meetings have worked over the years to develop ANSI and ASTM standards. As I noted at the MRF symposium in October 2008, I think our work was a benchmark in that it and the NIOSH Criteria Document (1998) codified the work to date, and our report provided a trajectory for the future.
There has been some talk in the MWF community about reactivating MWFSAC. The Federal Advisory Committee Act (FACA) regulates the actions of any such committee. FACA rules require a charter and a time limit for advisory committees. Our charter expired in August 1999, so the committee doesn’t exist anymore. Members of our committee collectively volunteered more than 3,200 hours for MWFSAC meetings, and this total does not include the chairperson’s time organizing meetings and writing the report.
Having people repeat this adventure would be a challenge. Would the results and recommendations be any different? Would OSHA take our advice and, if so, how long would it take the agency to act? These are daunting questions for anyone who thinks about reactivating the committee.
Figure 2. Dr. Sheehan is shown demonstrating problems that can occur when measuring air velocity (in this case for a lab hood).
TLT: Where do we go from here?
Sheehan: Debates about whether to regulate or not and the cancer issue should not continue to delay action to protect workers. No one debates the fact that misused or mismanaged metalworking fluids can harm workers, can have other environmental consequences and will waste the user’s money. This consensus should be the foundation of action for fluid formulators/suppliers, users, researchers and government agencies.
In some workplaces such as unionized auto plants of the Big Three, an internal exposure limit is part of contractual agreements. Most workers do not have this amount of protection, and we know having an exposure limit isn’t enough to protect workers.
Voluntary programs may work in big facilities hiring big reputable fluid suppliers who provide good product stewardship. But what happens in small facilities? How does an economic downturn affect worker protection? Fluid management should be a priority to save money, but with all a plant manager has to worry about in today’s economy, fluid management likely will not be a top priority. I anticipate less vigilance about fluid management and worker protection unless the Obama administration puts more focus on worker health and safety.
I recommend the following, and I believe that fluid formulators/manufacturers, their major customers and the industrial hygiene profession need to take the lead to:
1.
Mandate the use of a high quality systems management program as part of the contractual relationship between a fluid supplier and user. If the user is not going to manage or have the supplier manage the fluid correctly, suppliers shouldn’t sell to them (this can reduce third-party lawsuits!).
2.
Develop simple, online record-keeping systems, including fluid type, product name, product term of use, product volumes used, MSDS and locations within a plant where MWFs are used along with a mechanism for reporting and flagging fluid-related health incidents and triggering sampling (mist and fluid for suspect chemical and biological components). This would aid in tracking potential problem fluids, detecting illnesses early and potentially linking cause and effect. It also will have the day-today financial benefit of helping with inventory and purchasing.
3.
Pressure OSHA and/or NIOSH to develop agreements with machine tool equipment manufacturers to assure that new machine tools are only sold with complete enclosures (this could be similar to the asphalt pavers’ agreement of the 1990s).
4.
Until Item 3 is accomplished, strongly encourage industries purchasing new machine tools to use contract specifications limiting purchases to completely enclosed machines (labor-management contracts at facilities using machine tools could also include this requirement for machine tool specifications).
5.
Expand the certified MWF managers program and make this certification a job requirement for anyone responsible for fluid systems over a defined size.
6.
Mandate real
accountability in MWF stewardship programs and expand these programs to more industries and industrial sectors. Accountability should include barring companies that do not use good practices from reputable trade organization stewardship programs.
7.
Develop better procedures for cleaning out contaminated systems, removing biofilms and reducing the overuse/misuse of biocides.
8.
Continue improving exposure-assessment methods but focus on disseminating guidance about what method is appropriate to use in which situation and urge OSHA to update the best practices to include the NIOSH 5524 method, which is generally accepted as the best practice for exposure assessment.
9.
Encourage NIOSH to develop a database of MWF exposures in various industries and share health and exposure data across industries and sectors while maintaining individual-level privacy.
10.
Fund more epidemiological and toxicological research, especially in industries other than the auto industry, and have open sharing of existing data.
11.
Spend less money on litigation and regulatory obstruction and more on education by expanding training and outreach to provide a continuum of care. Instigate a paradigm shift by teaching apprentices in technical schools through engineers at universities so the next generation of machinists, machine operators and industrial engineers and managers know how to do systems management of MWFs.
12.
Encourage more integration of various programs and efficient use of funds by reinvigorating the Friends of the Metalworking Fluids community with more frequent symposia or other activities (including Web sites) to share ideas, enhance collaboration, foster cooperation and benefit workers and management.
13.
Work to bring balance and better functionality to OSHA. Voluntary programs can be great and have their place, but the pendulum has swung too far away from OSHA’s regulatory role—we don’t want to wait until some horrible workplace tragedy strikes to realize we need an efficient, engaged, competent and empowered regulatory agency doing its job of protecting workers and providing an even playing field for all industries.
Before the MWFSAC was even an idea, many members of STLE were part of an eclectic group, Friends of Metalworking Fluids, and helped crystallize consensus about many important issues such as systems management. We will need consensus, collegiality and a can-do spirit to make sure that machining processes involving MWF can be successful in the most important way possible—that those who work with MWFs return home every workday healthy and safe and have a lifetime of good health.
You can reach Dr. Maura Sheehan at msheehan@wcupa.edu.