Tilting at Wind Turbines
Dr. Robert M. Gresham, Contributing Editor | TLT Lubrication Fundamentals February 2009
We all agree that this is a wonderful new energy source, but more than a few technical issues must be resolved before it reaches full potential.
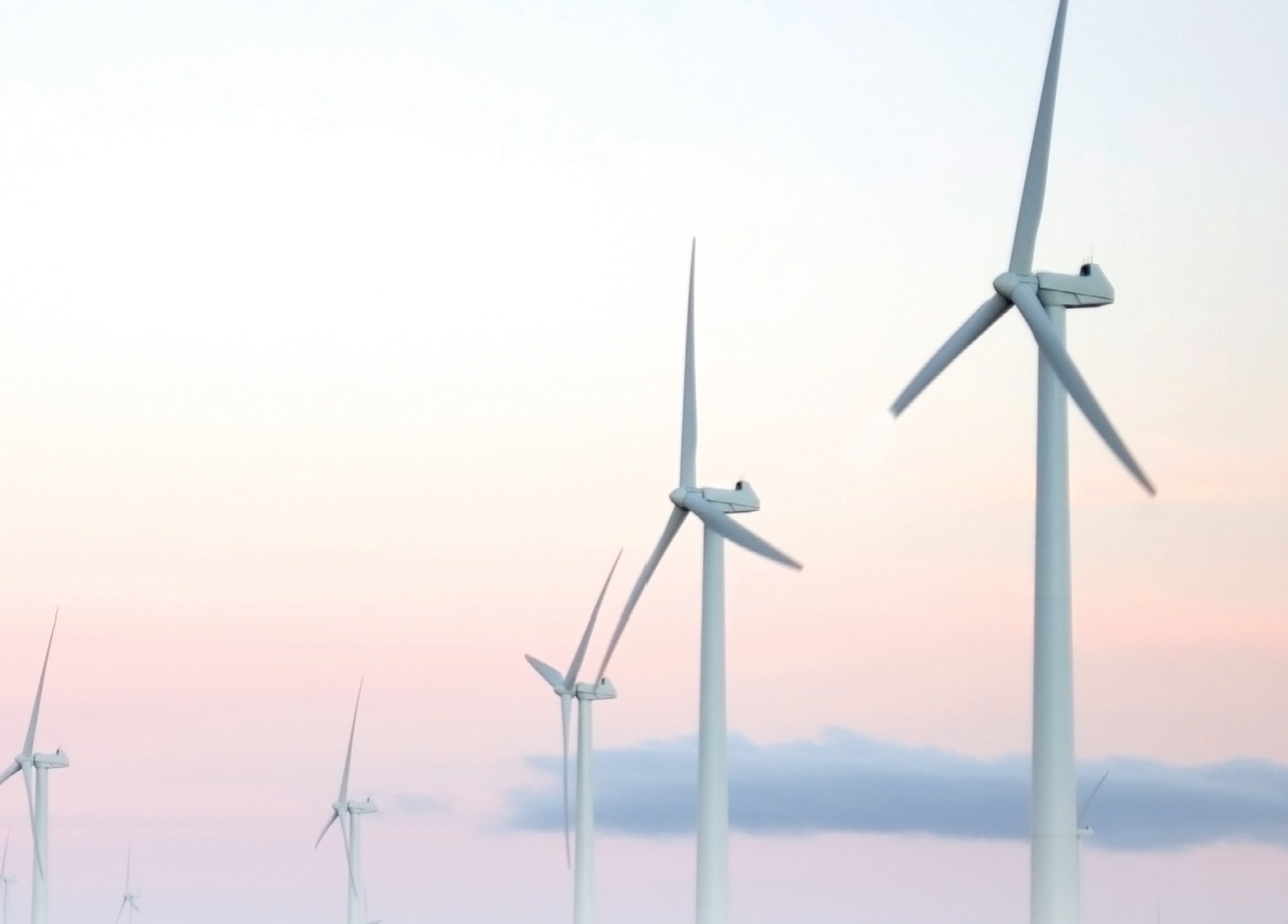
www.canstockphoto.com
KEY CONCEPTS
•
Energy experts hope to increase the amount of electricity generated by wind turbines from its current 2% to 20% by 2015—an ambitious goal.
•
Most electricity in the U.S. is needed on the coasts, which means it makes more sense to place wind turbines in the oceans.
•
Blade design, gearbox ratios and cost-effective condition monitoring are all engineering issues that must be resolved.
I would be less than honest were I to say that I have not been a bit skeptical of the whole wind energy issue. I can’t help feeling a little Don Quixotesque in imagining the great swirling giant’s arms preparing for my charge at this wind energy deal. My kids sometimes suggest that I might be a troglodyte, as well.
So what are the issues?
At last October’s International Joint Tribology Conference, cosponsored by STLE and ASME, I had something of an epiphany as I heard a distinguished group of experts make their presentations. More important, there was a discussion afterward where folks like me could ask their stupid questions and get reasoned answers.
So let’s start with the energy itself.
We are talking about electricity generation. Electricity can’t be stored and needs to be transferred to points where it is needed. So when we talk about wind supplying some percentage of the nation’s energy, we are talking about its electrical energy needs—still an enormous number but not as daunting as replacing all forms of our energy needs.
According to one of the panelists, Greg Ziegler with SKF, our electricity breaks down as follows: coal is 50%, gas 22%, nuclear 20%, hydro 7% and wind 2%. The goal is to increase wind to 20% by 2015. That is a pretty impressive growth industry by any standard.
The skeptic in me says follow the money. According to Sandy Butterfield with the National Renewable Energy Laboratory in Boulder, Colo., the cost of installation is as follows: wind $1,900 per KW vs. $1,800 for coal and $9,000 for nuclear. So the cost of installation is in the game. Indeed, the world’s largest supplier of wind turbines, Vesta in Germany, cranks out a new turbine every 45 minutes. So clearly there is a global business commitment to the wind industry.
The next key issue is that we already have an electricity transmission grid pretty much in place, but it is a little antiquated and, more important, not oriented toward locations where there is consistent wind. So there is a significant need to upgrade the grid system.
And where is that wind? I’ve been skeptical that there was even close to enough wind for this pipe dream to be a reality. Turns out that the western Midwestern region from western Washington, Montana and the Dakotas south through to north Texas has pretty consistent wind. Wind farms in this area are pretty isolated, perhaps destroying the view for farmers and ranchers but otherwise not a problem for grazing. But this isolation increases maintenance costs, especially in winter.
When one thinks a little deeper on the location of wind and the need for electricity, Mr. Butterfield makes the point that we need most of our electricity on the coasts, so it is actually more logical to have most of our wind farms in the oceans where there is plenty of open space, in fact, two-thirds of the earth’s surface. This has a lot of advantages and a few disadvantages. First, the water has to be relatively shallow (less than 20 meters) or else we’ll have to invent huge floating wind farms. This is doable, based on technology learned from offshore drilling, but surely will add to the cost.
When one thinks globally there is less of a negative environmental impact, at least once these floating farms are built. As any sailor knows, there are many areas on the oceans where there is almost always plenty of wind, like the trade wind belts and other such areas. If far enough out to sea, wind farms are not an aesthetic problem, except to the passing yacht or cruise ship.
What about engineering issues? According to Mr. Butterfield, who has been involved in this for 20 years, we have not yet optimized the designs. Indeed, I think we actually have a long way to go.
First, the early wind turbines, located near where I live in the Indianapolis area, primarily are powering rest stops on interstates. These are pretty noisy. We know that by varying blade pitch we can run the fan blades at a constant speed with tip speeds around 80 feet per second. This greatly reduces noise and results in a relatively slow-speed, high-torque machine that creates a relatively constant electrical output with less stress on the hardware.
We haven’t optimized the size of these machines. They are getting larger and larger. As a result, today’s wind turbines are even more intimidating than those of the Senior Quixote. The largest that I’ve read about have individual arms of 124 meters, similar to the one shown in Figure 1 from a photo in a recent article by
OilSpot News, published by DTN. Notice the relative size of the ship in the foreground. The trend, especially for ocean wind farm turbines, is toward colossally large machines.
Figure 1.
Given that we haven’t optimized the size of these machines, what are some of the other engineering issues? Well, this is one of the areas where life is not what it needs to be. The design goal for wind turbines is 20-30 years. From an investment standpoint we are looking at a goal of a 6-7 year payback. The reality is that we are having maintenance problems in the 3-5 year period. As we heard at the 2008 STLE Annual Meeting & Exhibition in Cleveland, blade design and control has evolved to a pretty high level allowing for very efficient capturing of the wind’s power, as well as helping to control speed and torque and is still ongoing.
For the most part the blades seem to be working pretty well; the issues now mostly relate to increasing efficiency. In addition, we find that the electrical generator is not a major problem. Further, we hear from grease expert Dr. Chuck Coe with ExxonMobil that the main rotor bearings, pitch and yaw bearings and generator bearings are all grease lubricated and perform well. These bearings, depending on location, can see temperatures from -30 C to as high as 100 C.
The grease, specially blended for this application, is based on a VG 460 oil. At the present time the weak spot in the overall design are the gearboxes. Also, the design pressures on the gearboxes are toward progressively higher ratios from a current high of 30:1 to 50:1. The trend is toward less massive gearboxes as well. Current gearboxes, similar to the one shown in Figure 2, can be larger than a Volkswagen. All this adds more and more stress on the gearbox.
Figure 2.
It goes beyond the scope of this kind of article to go into the intricacies of the design problems, but two key issues have emerged that are near and dear to tribologists and lubrication engineers.
First, existing and future turbines could greatly benefit from a proactive maintenance program that includes rigorous attention to contamination control and a sophisticated condition monitoring program involving remote sensing and transmission to wind farm control centers. All stuff we (STLE kind of folks) pretty much know how to do.
The second issue involves second generation designs of wind turbines. These new turbines, huge in size, can involve as much as 25 GW capacities. They would benefit from reliability-centered design techniques, coupled with reliability-centered maintenance. Indeed, the wind turbine community needs to involve tribologically oriented folks with this emerging industry from A to Z.
Sure, there are outside factors affecting this industry, including the recent results of our national election. However, this is a global business. The train seems to have left the station, so the U.S. will either be onboard as a leader or follower but involved either way. The turmoil in the financial markets may slow investment in this technology but is not likely to stop it.
As we go forward, I think you can look to more involvement by STLE and its members in this growing industry—and not by tilting at the flailing giant.
Bob Gresham is STLE’s director of professional development. You can reach him at rgresham@stle.org.