20 Minutes With Dr. James R. Anglin
Thomas T. Astrene, Publisher | TLT 20 Minutes February 2009
This Alcoa senior scientist examines the critical application issues with process and machine lubricants in the aluminum industry.
PROFILE:
Education
• Doctorate, Massachusetts Institute of Technology, Cambridge, Mass., Inorganic Chemistry (1974).
• Bachelor of Science, Queen’s University, Kingston, Ontario, Canada, Engineering Chemistry (1969).
Professional experience
• Senior Staff Scientist, Alcoa Inc., Alcoa Center, Pa., (1986-Present)
• Senior Research Scientist, The Elco Corp., Cleveland, Ohio, (1986)
• Research Chemist, Gulf Research & Development Co., Harmarville, Pa. (1978-1985)
• Visiting Assistant Professor, Bucknell University, Lewisburg, Pa. (1977-1978)
• Postdoctoral Fellow/Research Associate, University of Alberta (Edmonton), (1974-1977)
Professional affiliations
• STLE (Member/Corporate Member Representative since 1986)
• Certified Lubrication Specialist
• Chairman, STLE Nonferrous Council (2007-2008)
• Chairman, STLE Pittsburgh Section (2007-2008)
• Technical Editor, TLT Magazine
• American Chemical Society
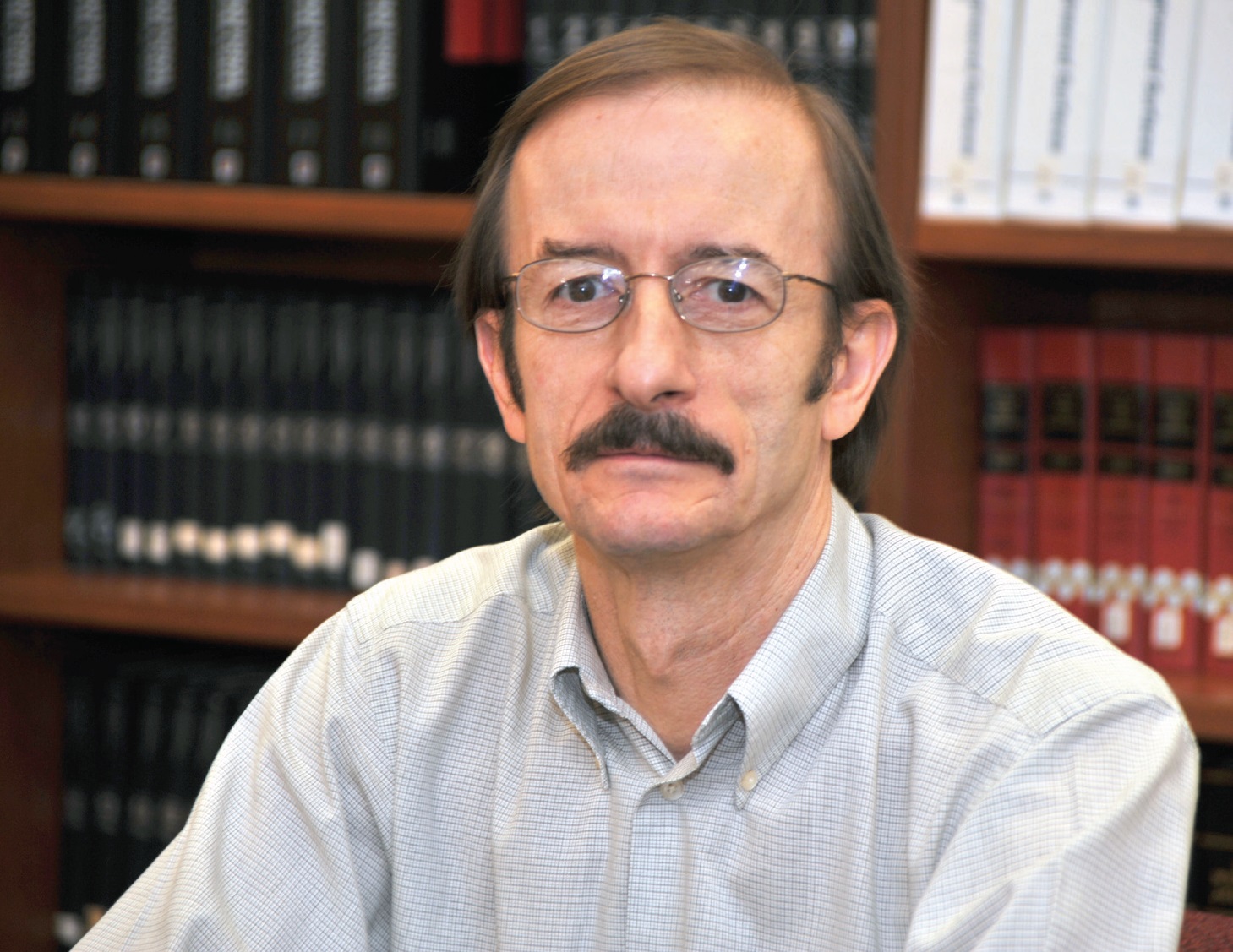
Dr. James R. Anglin
TLT: Provide a brief summary of your career with Alcoa.
Anglin: My career has focused on process lubricants and on machinery lubricants used in the aluminum industry. Process lubricants are needed not only for the rolling process but also for various hot and cold forming processes and for casting.
The work on machinery lubricants, which are used in the process equipment, has focused on the specification and approval of suitable products meeting the diverse needs of those processes. It has also extended to dealing with the troubles machinery lubricants can cause upon leaking into process lubricants. Developments are driven by meeting technical requirements, maintaining cost effectiveness and meeting or exceeding environment, health and safety regulations.
TLT: How did your background prepare you for your current career in tribology?
Anglin: The strength of my academic background is in chemistry, especially synthetic chemistry involving coordination compounds and organometallic compounds that are at the interface of organic and inorganic chemistry. My earlier industrial experience focused on products from petroleum and other hydrocarbon sources, along with the synthesis and evaluation of additives for them. It provided a good introduction to the properties and the testing of these materials. However, I had no experience in aluminum processing or the performance of lubricants at temperatures typical of hot aluminum metalworking, and this needed to be learned as part of my work at Alcoa.
TLT: What have been some of the biggest challenges in successfully implementing new process lubricants?
Anglin: As with many lubricant systems, aluminum process lubricants, such as those used in rolling, must meet a considerable number of requirements beyond simply being good lubricants. Integrating all of these requirements into the lubricant chemistry and the associated application and handling systems can be complex and require the collaboration of a number of disciplines. Experienced metalworking lubricant formulators are familiar with most of these requirements, but I would like to make a few comments on some that are specific to our work.
To begin with, for metal to be used in food, beverage and drug packaging, the lubricant chemistry needs to be selected in keeping with regulatory requirements such as FDA in the U.S. Additional requirements can include compliance with religious dietary requirements, the absence of allergens and the meeting of CONEG (Coalition of Northeast Governors) requirements as well as California Proposition 65 requirements.
Lubricants that are present on metal supplied to the customer also must be carefully formulated. For example, products called reoils and post-lubricants are applied to aluminum sheet to assist in forming products, including beverage and food containers, at customer plants. A key for these materials is the need to avoid imparting undesirable taste, odor or other unwanted attributes to the packaged products. One example of the importance of this property is the well-known association of undesirable taste in beer to parts per billion levels of unsaturated aldehydes that can form upon degradation of materials containing linoleates.
Lubricant residues are linked to a number of other product quality concerns. The residues can help protect the metal during shipping and handling; however, for food applications, the amount and composition must meet FDA requirements. They can impact the successful manufacture of laminated products and influence downstream operations such as conversion coating, painting and welding of sheet product. One remedy is cleaning of the metal product by any of a number of approaches.
Lubricants also play a significant role in determining a metal product’s appearance, which is an increasingly important attribute in the marketplace. Lubricant chemistry, for example, will influence adhesive wear between tooling and workpiece in the forming process and thus affect surface appearance.
The chemistry also can influence the amount and size of debris generated in the rolling contact. Significant levels of debris on the metal surface can cause it to appear dirty. Appearance is also affected by lubricant viscosity and the influence of temperature and pressure on it that control the film thickness in the contact area and, ultimately, the surface topography of the metal. As the ratio of film thickness to metal surface roughness increases, topography of the rolled metal changes and typically takes on a duller appearance.
Rather than extend the discussion to provide a relatively complete list of requirements for these fluids, let me simply emphasize the need to have excellent environmental, health and safety practices in place with any new product or process. This, together with a very compelling commercial need, is important for maintaining the engagement of plant personnel who must do the work of lining out their processes with the new product.
Figure 1. (a) Jim Anglin testing the exposure of a small sample of hydraulic fluid to a flame, while monitoring the continued combustion of a hydraulic fluid sample after removal from the flame, as shown in Figure 1 (b).
TLT: You mentioned the trouble that machinery lubricants can cause upon leaking into process fluids. Would you care to elaborate?
Anglin: It sounds pretty simple to instruct the operators of very complex processing machinery to upgrade their maintenance practices to eliminate leaks, but the reality is that this is a very difficult goal. The numerous hydraulic fluids, gear oils and other mill lubricants all have the potential to commingle with the process lubricants, whether in the form of simple leaks or mist. It’s not unheard of for cleaning chemicals or fire-suppressant materials to find their way into the process fluids. On the other hand, it’s also possible for the process fluids to contaminate certain machinery lubricants and affect their performance.
The leaking of machinery lubricant can be problematic in a number of ways. A simple leak can lead to increased cost by requiring makeup oil to be added to the system and raising environmental, health and safety issues where it leaks. If the leaked fluid enters a process lubricant that is expected to provide consistent performance over a lengthy time period, the result is typically a degradation of performance. The potential problems are numerous and include changes to the viscosity and boundary lubricant performance of the process lubricant as a result of simple mixing or chemical reaction with the contaminant. For emulsion products, contamination can affect their stability and thus their performance.
To address contamination problems, resources can be needed to reclaim the process lubricant if possible, or extra costs can be incurred for its premature disposal and replacement. The presence of machinery lubricant in the lubricant residues on rolled product can be one source of FDA concerns. It also can lead to undesirable staining of annealed products, a well-known problem in the industry.
TLT: What fluids do you recommend for use near ignition sources?
Anglin: With Alcoa’s commitment to safety, it’s natural to expect great attention to the safe use of hydraulic fluids in metal-processing applications. These applications can involve the use of fluids at high pressures in the proximity of hot and even molten aluminum in such processes as casting, rolling, forging and extrusion. Temperatures of concern range from ~260 C to ~740 C for these processes but are yet higher for smelting operations. For safe operation, it is important to eliminate leaking of lubricant onto hot surfaces, such as slabs of hot metal in the hot rolling process, as well as sprays that could contact ignition sources.
What we have confirmed in our work evaluating the safety performance of commercial fluids is that anhydrous fluids are currently available that resist burning very well at temperatures up through at least 740 C. These fluids, which are arylphosphate esters, can continue to resist ignition even as temperatures reach aluminum casting temperatures.
In our testing of ISO 46 products as reported at the 2008 STLE Annual Meeting in Cleveland, all other anhydrous fluids examined, including various organic esters, polyalkylene glycol and mineral oil, ignited in contact with metal surfaces at temperatures representative of hot aluminum metalworking. Among the other anhydrous fluids, mineral oil was usually but not always the weakest performer in this testing.
The resistance to ignition of the other anhydrous fluids varied considerably, but in all instances was limited to a portion of the temperature range of concern. Beyond that, the fluids would burn, with the intensity of the burning increasing with increasing temperature. A similar study of selected water-containing fluids that were over 50% organic content did show some potential safety advantages such as an increased delay before ignition occurred, but these would ignite once sufficient water had boiled away.
Spray flammability testing is also important in evaluating fluid safety because of the heightened danger associated with spray flames. Common test protocols involve passing atomized fluid through a flame and monitoring its burning under standard conditions. Fluids with significant contents of water were excellent performers in our spray flammability testing.
However, in our plant processes, it is my belief that hot surfaces represent the main ignition sources for hydraulic fluids since flames are not commonly present except in limited situations, such as forging with organic die lubricants. From this premise, the likelihood of generating a hazardous spray flame is related to the likelihood of the spray fluid igniting on the hot surfaces present. Beyond that, the spray flame characteristics of the fluid then come into play. Two factors that can affect the spray flame intensity are the heat of combustion of the fluid and the presence of additive that successfully limits the formation of readily ignited fine spray droplets.
Safe handling of fluids near ignition sources needs to include engineering rigor to (1.) minimize the likelihood and the amount of any leak, especially sprays and (2.) limit the potential exposure of plant personnel to fire and fumes. Proper attention to safety also requires being proactive to ensure that the level of fire resistance of an in-use fluid is not compromised by contamination, degradation or poor attention to maintenance such as not maintaining the proper amount of water in a water-glycol.
I would like to see continued work by current and potential fluid suppliers to provide products with excellent resistance to burning, especially in scenarios related to our industry, together with strength in other areas such as wear performance, ease of maintenance and cost effectiveness.
TLT: Have environmental, health and safety regulations played a significant role in your career?
Anglin: Yes, it’s gratifying to have made contributions that can be beneficial both commercially and in the environmental, health and safety areas. This includes forging lubricant reformulation for improved hygiene and emissions performance, the development of post-lubricant technology that enabled reduced VOCs in their use and the development of technologies that minimize losses of rolling fluids to the environment. It also has included projects to respond to changes in the raw material supply chain while maintaining compliance with air emissions regulations.
TLT: Do you have any closing comments?
Anglin: The industry’s production equipment is being continuously challenged to provide more cost-effective performance. Process and machinery lubricants will continue to play a key role in this challenge while meeting increasingly strict environmental, health and safety requirements as part of a sustainable production vision. Where plant leadership embraces the need to move forward with improved products and processes, they deserve to be commended.
You can reach Jim Anglin at james.anglin@alcoa.com.