History’s ultimate lube job
Dr. Christopher DellaCorte | TLT Guest Editorial January 2009
Greasing mechanisms on the International Space Station involved working 250 miles above Earth at 17,400 miles per hour.
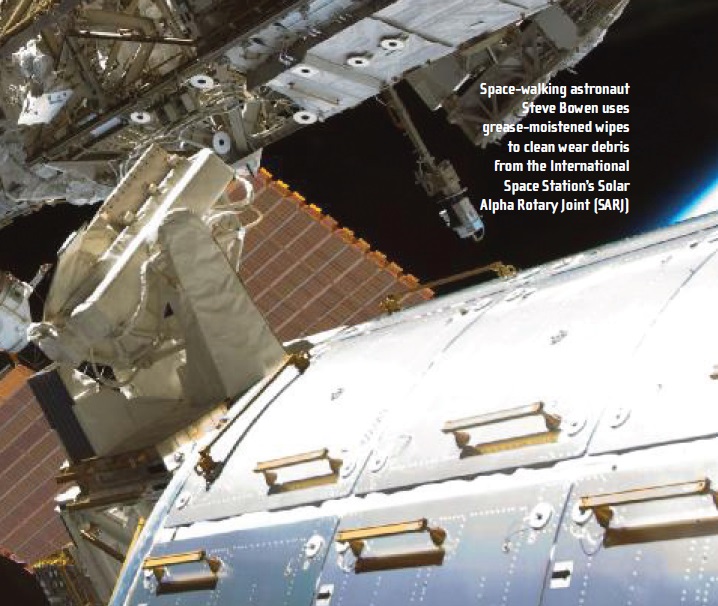
Space-walking astronaut Steve Bowen uses grease-moistened wipes to clean wear debris from the International Space Station’s Solar Alpha Rotary Joint (SARJ).
Last November many of us in the tribology community followed what is likely the most extreme lube job in history: greasing critical mechanisms while floating outside the International Space Station.
I watched this dramatic event closely for several reasons. First, I am one of NASA’s few tribologists and have a long history of aerospace lubrication experience. Second, I have been intimately involved with troubleshooting the Canada Arm’s stiff wrist (aka Latching End Effector or LEE). Third, I am also a member of the root cause analysis team for the failed starboard side rotating bearing that supports the station’s massive solar panels (aka the Solar Alpha Rotary Joints or SARJ), allowing them to track the sun. Finally, I am intrigued by the concept of the ultimate lube job—sending astronauts into space to lubricate balky mechanisms.
I sat glued in front of my computer watching a live video stream of space-walking astronauts Heidemarie Stefanyshyn-Piper, Steve Bowen and Shane Kimbrough, grease guns in hand, adding liquid lubricants (grease is really a mixture of oil, thickeners and additives) to bearing surfaces originally designed to operate solely under solid lubrication.
The Canada Arm’s LEE has been suffering with cables that wouldn’t fully return to their rest positions due to binding spherical-rod end bearings. These small, thumbnail-sized bearings experience little or no load when operating and were thought to require only minimal lubrication for long life. A simple burnished film of solid lubricant applied during initial assembly was found sufficient in life tests.
Unfortunately, on orbit the cable ends began to bind prematurely. Recent ground trials showed that a dab of grease applied to the parts, accompanied by wiggling of the cables to spread the lubricant, enabled enough oil to penetrate and loosen the bearings. If you were watching the space walk you might have seen Shane Kimbrough exercising the cables after greasing them to work the lubricant inside. Early indications suggest this lube job was a success.
The SARJ lube job was a great deal more complex. First, copious wear debris had to be removed using grease-moistened wipes. Then damaged rollers were replaced, and grease was applied to the raceway surface. This sounds simple enough, but bear in mind these folks are confined inside stiff, bulky pressurized space suits while floating 250 miles above the earth streaking across space at some 17,400 miles per hour!
Like the Canada Arm, the SARJs were designed to run dry, employing precise rolling contact combined with thin gold solid lubricant plating on the rolling elements to provide low friction and long life. Unfortunately, for reasons still under study, the solid lubricant was inadequate, leading to excessive friction that triggered unanticipated high kinematic loads that damaged the running surfaces. The grease applied in orbit should lower the friction below the threshold for further damage and allow limited joint operation until more permanent repairs can be made.
Though these two problems represent tribological failures, I find the efforts of these countless engineers, technicians, astronauts and tribologists inspiring. These folks dug in to understand the problems and fix them in space.
I just wish I could have convinced NASA management to send me up there for the most extreme lube jobs ever done!
Chris DellaCorte is an engineer with NASA Glenn Research Center in Cleveland. He is a member of STLE’s board of directors and was TLT editor from 2003 to 2007. You can reach him at christopher.dellacorte@nasa.gov.