20 Minutes With Dr. Arup Gangopadhyay
Karl M. Phipps, Managing Editor | TLT 20 Minutes January 2009
This Ford Motor Co. engineer employs a variety of techniques to solve the automotive industry’s toughest lubrication challenges.
Profile:
Education
• University of Minnesota, Minneapolis. Doctorate in Metallurgical Engineering, 1985.
• Indian Institute of Technology, Kanpur, India. Master of Technology in Metallurgical Engineering, 1982.
• Bengal Engineering College, Kolkata, India. Bachelor of Engineering in Metallurgical Engineering, 1979.
Professional experience
• Ganopadhyay started his career as a research fellow at Northwestern University’s Center for Engineering (1985) and at the National Institute of Standards and Technology (1988-89). He later worked for Ford Motor Co.’s Scientific Research Laboratory in Dearborn, Mich., serving as technical specialist (1989-1995) and senior technical specialist (1995-2003). Since 2003 has served as technical leader for Ford Motor Co.’s Research and Innovation Center.
Professional affiliations
• Vice Chairman, STLE Annual Meeting Program Committee, 2008-09
• Chairman, STLE Gears and Gear Lubrication Technical Committee, 2002-2004
• Chairman, STLE Ceramics and Composites Technical Committee, 1992-1996
• Board member, STLE Detroit Section, 2000-Present
• Chairman, ASME Awards and Honors Committee, ASME Tribology Division, 2003
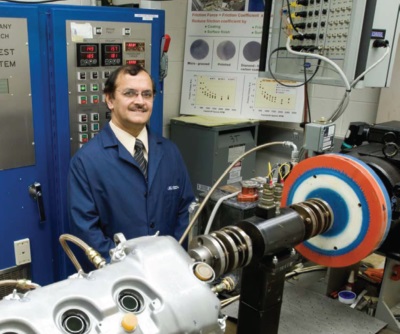
Dr. Arup Gangopadhyay
TLT: How did you become interested in tribology?
Gangopadhyay: While finishing up my doctorate at the University of Minnesota, I was exploring some post-doctoral opportunities. My doctorate work was related to wear mechanisms of grinding media used for ball milling operations to crush taconite ores into finer particle sizes. This work involved studying both abrasive and corrosive wear since grinding is done under wet conditions. This is where I developed knowledge and experience in wear, although I did not know much about friction, lubrication or other nonferrous metals.
Meanwhile, I applied for a research fellow position at Northwestern University’s Center for Engineering Tribology and was hired to work with professor Herbert Cheng. This was my first exposure to tribology, as I worked closely with professors Cheng and Morris Fine and learned a lot about tribology of ceramic materials.
Later, I worked with Dr. Said Jahanmir at the National Institute of Standards and Technology and did research on solid lubrication of ceramics, which gave me a much broader experience in the field. In 1989 I joined Ford Motor Co. Since then all of my work has been related to automotive tribology.
TLT: What do you enjoy most about your job at Ford?
Gangopadhyay: I think what I enjoy most about my job is the opportunity to work with great people every day. In my technical group, we have people that come from diverse backgrounds in mechanical and chemical engineering, physics and chemistry. Everybody looks at a problem from different angles, which makes discussing tribology very interesting.
On a daily basis I interact with many talented, highly skilled and knowledgeable professionals in different areas ranging from lubricants, engine systems, transmission systems and axles. I’m always learning new things from people, which helps in brainstorming ideas for projects that will, we hope, address the current and future needs of the company. In addition, our group also interacts regularly with oil and additive companies that keep us up to date on technologies they are working on and what they think may help us to produce better quality products.
TLT: What kind of tribological research or projects are you currently working on?
Gangopadhyay: The goal of our work is to improve fuel economy and power train component durability through the use of novel materials and surface engineering, as well as to improve our understanding of how lubricant additives interact with surfaces. This covers both the short and long-term needs of the company and also includes a blend of basic and applied research.
Improved fuel economy of our vehicles is the top priority of our customers, especially in light of rising gas prices. We see Ecoboost, where we use a turbocharged direct injection gasoline engine, as one of the main drivers for fuel economy improvements. Increased use of six-speed automatic transmissions, electric power steering system and weight reduction also would help further improve fuel economy.
Tribology plays a part also. We are looking into various types of engineered surfaces, including mechanical texturing, laser dimples and lines, surface roughness optimization and various ways of shot peening to reduce friction at valve train components and piston rod assembly (
see Figure 1). There are still opportunities to reduce friction at these contacts, although the improved fuel economy may not be as big as some of the technologies I mentioned before. But we are looking at every opportunity however small it may be. The advantage of some of the tribological solutions is that they are quite attractive from a cost standpoint.
Figure 1. (a) Motored valve train friction data for a direct acting mechanical bucket type valve train as a function of camshaft speed. Surface engineering on bucket surface in contact with the camshaft significantly reduced friction. The tribological contact of interest is shown in Figure 1 (b).
We see an increased penetration of diesel light-duty trucks and passenger cars, and they will be equipped with a particulate filter on the exhaust pipe to trap soot particles to meet diesel emission standards. After a while, when the soot particles fill the filter, it will be necessary to burn off soot particles. This will be achieved by injecting fuel late in the combustion cycle to raise exhaust gas temperature. This is known as post-injection.
During post-injection some of the unburned fuel goes past the rings and collects on the oil sump. We are looking into the effect of fuel dilution on oil properties like oxidation, nitration, acid numbers, viscosity, friction and wear. Also, some of our customers may use biofuel. We are looking into the effect of biofuel dilution in oil, too.
Another project we are working on is understanding pitting in transmission gears—how to avoid it and what needs to be done to improve pitting resistance. This will help us transfer more energy through the exiting design and also extend the life of the system. We are looking into fluid formulation impacts and surface engineering.
TLT: Tell us what approaches you use to solve a tribological problem in your work?
Gangopadhyay: That’s an interesting question. I do not think there is any standard method for solving a tribological problem. You have to treat each problem and approach differently. For example, one of our product development engineers came to us with a problem related to brake fluid. Whenever the brake pedal was pushed, customers felt a vibration. Obviously, they were not happy. Upon further investigation, it was found that the vibration was coming from the master cylinder.
The master cylinder is a device in the brake line that boosts the pressure applied by the brake pedal. More specifically, the vibration was coming from the stick-slip motion of the plunger in the cylinder housing.
So the engineer talked to a few brake fluid suppliers to resolve the issue. The engineer was looking for a test method to evaluate which brake fluid would be the best. We did not have any particular equipment or test method to evaluate the brake fluid. Since it is a line contact between the plunger and the cylinder housing, we decided to use a cylinder on flat contact geometry in the Plint TE 77 machine in an attempt to capture the stick-slip phenomenon. Also, this machine was better suited because of reciprocal motion as seen in the master cylinder application.
We designed and conducted experiments to represent equivalent contact stress, stroke, frequency and temperature as closely as possible for this particular application. We did see stick-slip phenomenon, and there was differences between the fluids. Also, the results correlated with our experience in the field. So, we were able to help select the right fluid. We also learned a lot about the brake fluid, something we did not deal with before.
Another example occurred when we were working on a valve train component to reduce friction through surface engineering. Our work focused on the upgraded version of an existing engine for future applications. All of our test data showed substantial friction reduction. We were excited because the particular type of surface could be easily manufactured in volumes. The question was raised if the same technology could be applied to future engine applications. Following similar tests with another engine hardware, we observed that it offered very little benefits. This was disappointing from a business standpoint because ideally we would have liked to use the same technology across many applications to reduce complexity and cost. However, we wanted to understand why the results were different. The engine oil technology was different between the two tests.
Following conversations with component and engine oil suppliers, it was becoming more evident that these two factors were not significant. We decided to use analytical tools to estimate friction using relevant hardware data. It turned out the asperity friction was higher with the first engine compared to the second one due to the applied maximum load and few other design features. Therefore, following surface engineering, it reduced asperity friction more in the first engine than the other and, hence, the difference in friction response. Therefore, for the second engine we needed to apply a different solution. However, it helped to understand the apparent discrepancy.
In my opinion, different problems need different approaches to find a solution. But the common step is understanding the operating conditions, the environment and the interactions between associated components.
TLT: What do you find to be most interesting in your research in studying gears and gear-related lubrication issues?
Gangopadhyay: Gears are one of the most critical components in the power train system that transfers energy from the engine to the wheels through transmission and axles. The requirements for transmission gears are very different from axle gears. Inside the axle housing there are gears of various sizes, and some of the gears have phosphate coating, while others are not dependent on the loads they bear.
If someone buys an F-150 truck and the next day they are towing 10,000 lbs. through hills, they may very well severely damage the gears unless the coating characteristics, surface roughness and lubricant formulation are designed right. The phosphate coating characteristics can greatly affect gear wear, as can the initial surface roughness. That is why we have a specification for the coating and the surface roughness. We pay a great deal of attention to break-in characteristics of gears and the lubricant formulation impact. Lubricant formulation also impacts the durability of friction clutch plates used for limited slip differentials and bearing durability. Therefore, we cannot look into gears in isolation. We need to look at the entire system, which includes gears, coatings, lubricants and clutch plates. It is the system approach that makes this area challenging and interesting.
TLT: Why do you think it is important to improve axle efficiency?
Gangopadhyay: As I said earlier, we are looking into all possible opportunities to improve fuel economy of our vehicles. Today’s consumers want high fuel economy vehicles. We believe improving axle efficiency will improve fuel economy.
First of all, axles run quite efficiently 95%-98% under high torque conditions such as towing. However, at low torque ranges, like starting from a traffic light or a stop sign, the efficiency could be quite low. We are trying to improve axle efficiency under these driving conditions through the use of reduced lubricant viscosity and improved surface finish of gears (see Figure 2). However, we need to make sure that durability is not compromised not only for gears but also for clutch-pack systems for the limited slip differentials.
Figure 2. Opportunity lies in improving axle efficiency under low torque operations by reduced lube viscosity.
Also, we need to ensure that NVH characteristics are not compromised, which may arise from stick-slip type situations resulting from the interaction of lubricant additives and clutch materials. Meeting all these requirements makes lubricant formulation quite challenging.
TLT: Has the nature of research changed since you joined Ford?
Gangopadhyay: Yes, it has changed quite a bit. In the early ’90s there was a lot of flexibility on the selection of research areas, as long as one could defend to management the path of relevance to our products and processes. For example, we had a group developing scanning tunneling microscopes. We anticipated that, if successful, the tool could be used to understand tribological processes and others at very fundamental levels. It was an exciting and scientifically challenging project. I also worked on a team that was developing diamond-like carbon films. We knew that these films could offer low friction coefficients resulting in reduced frictional losses.
We spent several years developing and evaluating these films for tribological applications. It was considered a success because it improved performances of certain components. Now scanning tunneling microscopes are used widely to study tribological surfaces, and diamond-like carbon coatings are used in automotive components. In the late ’90s, we started asking ourselves (a.) how can we increase technology transfer from research to our products? and (b.) what is the best utilization of our resources to be more competitive?
In this regard, we started asking for any research project and whether Ford should be doing this or a supplier. That significantly changed the scope of any research project and put more focus on technology development and increased collaboration with suppliers. This brought a significant shift from pure research to applied research. Then from the early to mid-2000s, we observed a shift toward advanced engineering.
Today, Ford is more closely aligned than before with product development and engineering to address its current and future needs. However, as a research organization, there are still opportunities to satisfy scientific curiosity as long as it is directly related to the products.
In today’s environment, I do not think we would be spending our resources in building instruments like scanning tunneling microscopes or developing a new coating. We would either buy it from a supplier or co-develop a coating with a supplier. However, even today we maintain a balance between research and advanced engineering to ensure we are not tilted heavily one way or the other. I believe this scenario is not typical of Ford but for other companies as well.
TLT: What advice would you share with young engineers and scientists interested in tribology?
Gangopadhyay: My advice to young engineers and scientists would be to have an attitude of continuous learning.
First, they need to develop a deep technical knowledge, which comes through indentifying the gap in our understanding and also through understanding how the system or components you are working on functions. Only then is it possible to think of possible solutions. However, it is important to recognize that the potential change or solution does not interfere with the operation of surrounding components, can be manufactured at an acceptable cost and cause no harm to the environment.
It is quite satisfying for researchers to see that some of the things they worked on implemented into products. Second, they need to be well informed of new technologies and trends that can be achieved through interactions with colleagues and by keeping up with the literature, including referred journals and magazines.
I would also recommend getting involved in STLE, either at the local section and/or at the national level. Most of the local sections arrange monthly technical meetings where they invite outstanding speakers to talk on various topics. This is a great opportunity to expand knowledge in areas outside one’s core expertise.
Editor’s Note: Dr. Gangopadhyay’s name was submitted for a 20 Minutes profile by STLE’s Gears and Gear Lubrication Technical Committee.
You can reach Arup Gangopadhyay at agangopa@ford.com.